Introduction
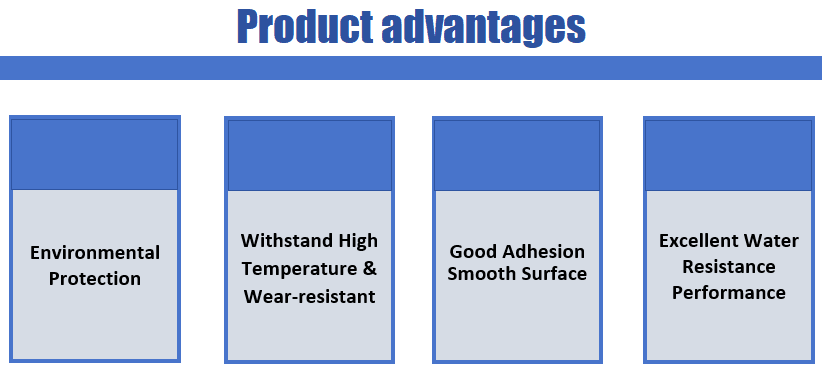
In the world of packaging and manufacturing, aluminum bonding adhesives play a crucial role in ensuring strong and reliable connections. These specialized adhesives are designed to bond aluminum surfaces effectively, making them indispensable in various applications. Understanding the different types of aluminum bonding adhesives available is essential for anyone involved in product development or packaging solutions.
Understanding Aluminum Bonding Adhesives
Aluminum bonding adhesives are formulated specifically to adhere to aluminum surfaces, which can be challenging due to their smooth and often non-porous nature. From water born laminating adhesive options to traditional solvent-based choices, each type brings its unique properties that cater to specific needs. Whether you're considering a water born adhesive for PTP blister packaging or exploring aluminum adhesive sheets, grasping these nuances is key to achieving optimal results.
Importance of Choosing the Right Adhesive
Choosing the best glue for bonding aluminium is not just about convenience; it directly impacts the performance, durability, and efficiency of your final product. The right adhesive can enhance production processes while ensuring that bonded materials withstand environmental stresses over time. Therefore, understanding factors such as substrate compatibility and required cure times becomes paramount when selecting an aluminum bonding adhesive.
Overview of Applications in Packaging
The applications of aluminum bonding adhesives extend far beyond mere assembly; they are vital in creating secure seals in various packaging types. From food packaging that requires hygienic properties to consumer goods where aesthetics matter, these adhesives serve multiple roles across industries. By harnessing the advantages of water born aluminum foil adhesive or other variants, manufacturers can achieve both functionality and sustainability in their packaging solutions.
Types of Aluminum Bonding Adhesives
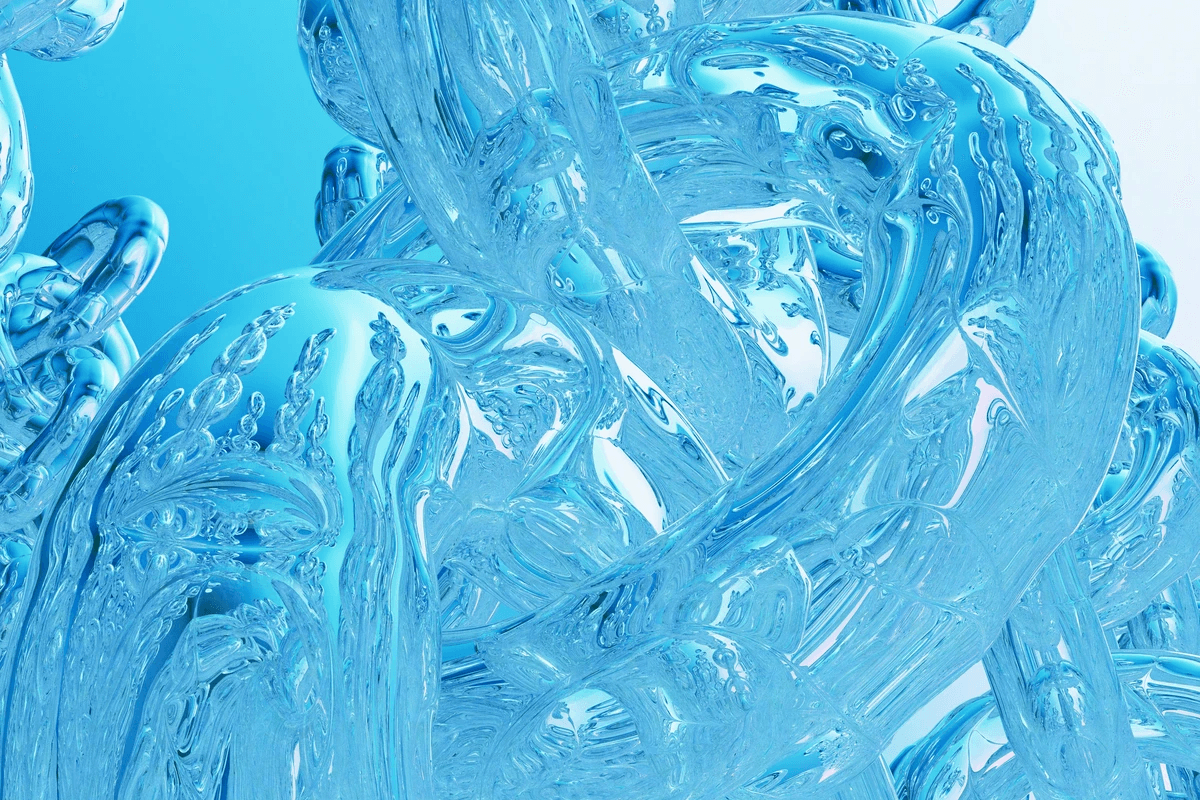
Water-Based Adhesives for Sustainable Choices
Water-based adhesives are gaining traction in industries focused on sustainability and environmental responsibility. These aluminum bonding adhesives utilize water as a solvent, making them less harmful to both users and the environment compared to their solvent-based counterparts. Not only do they provide excellent adhesion for bonding aluminum, but they also contribute to a greener future by reducing volatile organic compounds (VOCs) in manufacturing processes.
Choosing the best glue for bonding aluminium often leads manufacturers toward water-born options due to their eco-friendliness and versatility in various applications. For instance, these adhesives are particularly effective in packaging scenarios like PTP blister packaging where safety and performance are paramount. Their unique properties allow them to maintain strong bonds even under challenging conditions while ensuring compliance with environmental regulations.
Chemix's Water-Based Resin Solution
Chemix has developed a standout water-based resin solution that exemplifies innovation in aluminum bonding adhesives. This product not only boasts impressive adhesion qualities but is also designed with user-friendliness in mind, making it suitable for both professionals and hobbyists alike. The Chemix water-born adhesive excels at bonding aluminum surfaces seamlessly, providing a reliable alternative that doesn’t compromise on performance or sustainability.
One of the key advantages of this water born aluminum foil adhesive is its quick drying time, which enhances production efficiency without sacrificing bond strength. Moreover, it's versatile enough to be used across various applications including industrial uses where durability is essential, such as aluminum adhesive sheets used in construction or automotive sectors. With Chemix's solution, you’re not just choosing an adhesive; you’re investing in quality and sustainability.
Traditional Solvent-Based Options
While water-based adhesives are on the rise, traditional solvent-based options still hold their ground when it comes to certain applications requiring robust performance under extreme conditions. These aluminum bonding adhesives typically offer superior initial tack and faster curing times compared to water-based alternatives, making them ideal for high-speed production lines where time is money. However, it’s essential to weigh these benefits against environmental concerns associated with VOC emissions.
Aluminium glue welds created using solvent-based adhesives can provide strong bonds necessary for demanding environments—think heavy machinery or outdoor equipment exposed to harsh elements. However, choosing the best glue for bonding aluminium should involve considering not only performance but also safety regulations related to chemical exposure during application processes. As industries evolve toward greener practices, even traditional manufacturers are exploring ways to reduce their ecological footprint while maintaining high standards of adhesion.
Factors to Consider When Choosing Adhesives
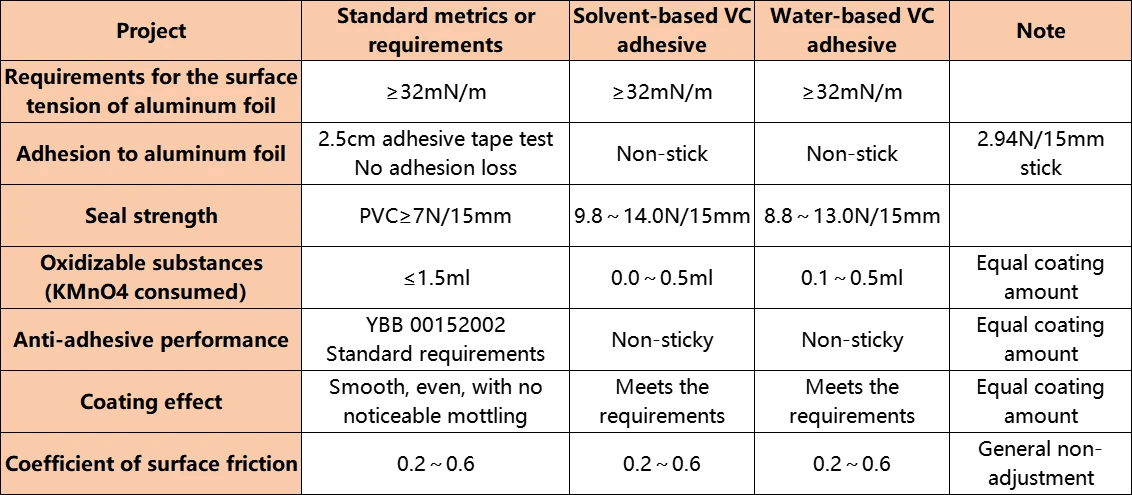
Substrate Compatibility for Effective Bonding
The first step in choosing an aluminum bonding adhesive is ensuring substrate compatibility. Not all adhesives work well with every type of aluminum; some may require a specific surface treatment or primer to maximize adhesion. By selecting a water born adhesive for PTP blister packaging or other applications that match your materials, you can enhance the performance of your bond and minimize issues down the line.
Moreover, understanding how different types of aluminum react with various adhesives is crucial. For example, while water born aluminum foil adhesive is excellent for flexible applications, it might not be suitable for rigid structures without proper testing. Therefore, always verify compatibility before committing to an adhesive solution.
Environmental Conditions Impacting Adhesive Performance
Environmental conditions play a pivotal role in determining which aluminum bonding adhesive will perform best in your application. Factors like temperature fluctuations, humidity levels, and exposure to chemicals can affect adhesion strength and longevity. For instance, if you're using an aluminium glue weld in a high-humidity environment, you'll want an adhesive specifically designed to withstand such conditions.
Additionally, consider how outdoor exposure might impact your choice of adhesives—certain formulations may degrade faster when exposed to UV light or extreme temperatures than others. Water born laminating adhesives often provide better resistance against environmental stressors compared to traditional solvent-based options due to their chemical composition and curing processes.
Required Cure Times for Production Efficiency
Production efficiency hinges on understanding required cure times when selecting an appropriate aluminum bonding adhesive. Some applications demand quick turnaround times; thus opting for fast-curing adhesives can significantly streamline operations without sacrificing bond quality. Conversely, if you have more time available during production cycles, exploring slower-curing options could yield stronger bonds in certain situations.
It's essential also to consider how cure times may vary based on environmental conditions—higher humidity or lower temperatures may extend curing periods beyond initial estimates. When evaluating different options like water born laminating adhesives versus traditional solvent-based choices, take note of how these factors affect overall production timelines and costs associated with delays.
Applications of Aluminum Bonding Adhesives
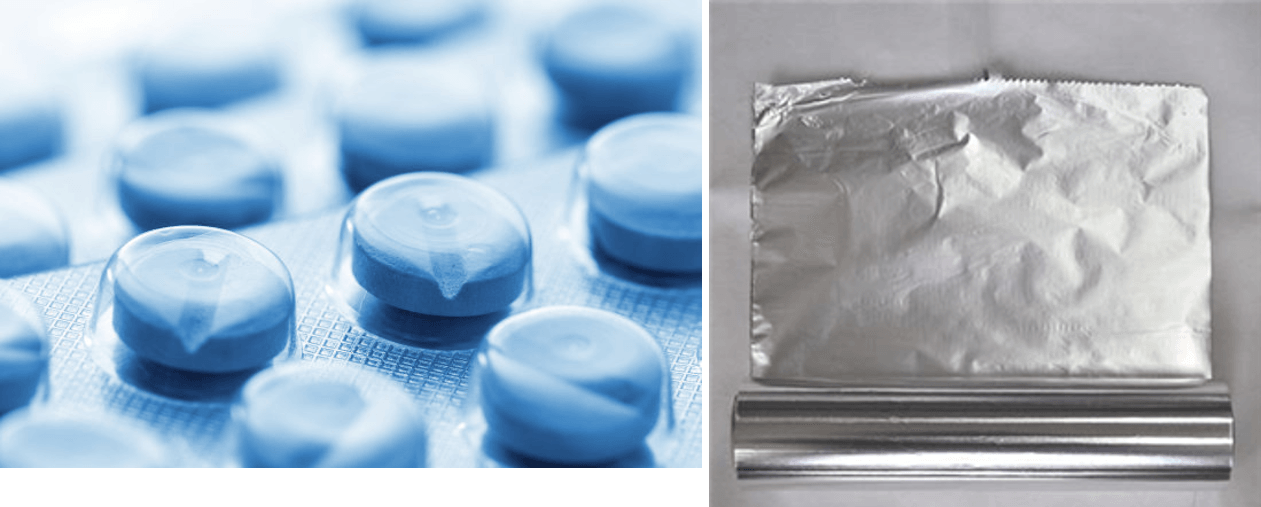
Aluminum bonding adhesives play a pivotal role in various industries, particularly in packaging, where their unique properties enhance the functionality and durability of products. These adhesives are specifically designed to bond aluminum surfaces effectively, ensuring that packages remain intact while providing protection against environmental factors. Understanding the diverse applications of these adhesives can help manufacturers make informed decisions when choosing the best glue for bonding aluminum.
Bonding Aluminum in Various Packaging Types
In the packaging industry, aluminum bonding adhesives are essential for creating airtight seals and maintaining product integrity. From food packaging to pharmaceutical applications, these adhesives ensure that aluminum foil and other materials adhere securely, preventing contamination and extending shelf life. Whether it's flexible pouches or rigid containers, selecting the right aluminum bonding adhesive significantly impacts performance and customer satisfaction.
The versatility of water born laminating adhesive has made it a popular choice among manufacturers looking for eco-friendly options without sacrificing quality. These adhesives can bond aluminum to various substrates while providing excellent flexibility and resistance to moisture. As businesses increasingly prioritize sustainability, water born adhesive for PTP blister packaging is gaining traction as a reliable solution that meets both performance standards and environmental requirements.
Industrial Uses for Aluminum Adhesive Sheets
Beyond packaging, aluminum adhesive sheets find extensive use in industrial applications where strength and durability are paramount. Industries such as automotive and aerospace rely on these sheets for assembling components, ensuring high-performance bonds that withstand rigorous conditions. The application of an aluminum glue weld can create robust joints that resist vibration and thermal expansion—critical factors in demanding environments.
Additionally, the use of water born aluminum foil adhesive allows manufacturers to streamline production processes while minimizing environmental impact. These adhesives provide excellent adhesion properties without harmful solvents, making them suitable for various industrial applications where safety is a concern. By leveraging advanced adhesive technologies like these, companies can improve efficiency while adhering to regulatory standards.
Benefits of Water-Born Laminating Adhesives
Water-born laminating adhesives offer a range of benefits that make them an attractive choice for many manufacturers seeking effective solutions for bonding aluminum surfaces. One significant advantage is their low volatile organic compound (VOC) content, which aligns with growing environmental regulations aimed at reducing harmful emissions during production processes. This characteristic not only promotes a healthier workplace but also appeals to eco-conscious consumers.
Moreover, water born laminating adhesive provides exceptional adhesion strength across different substrates while remaining flexible enough to accommodate material movement over time. This flexibility is crucial in applications where temperature fluctuations may occur or where products undergo stress during handling or transportation. By choosing this type of aluminum bonding adhesive, businesses can ensure long-lasting bonds without compromising on performance or sustainability.
In conclusion, understanding the diverse applications of aluminum bonding adhesives—from packaging solutions to industrial uses—enables companies to select the most appropriate products for their needs efficiently. With options like water born laminating adhesives leading the charge toward sustainable practices without sacrificing quality or effectiveness, it’s clear that innovation continues to shape this sector positively.
Pros and Cons of Different Adhesive Types
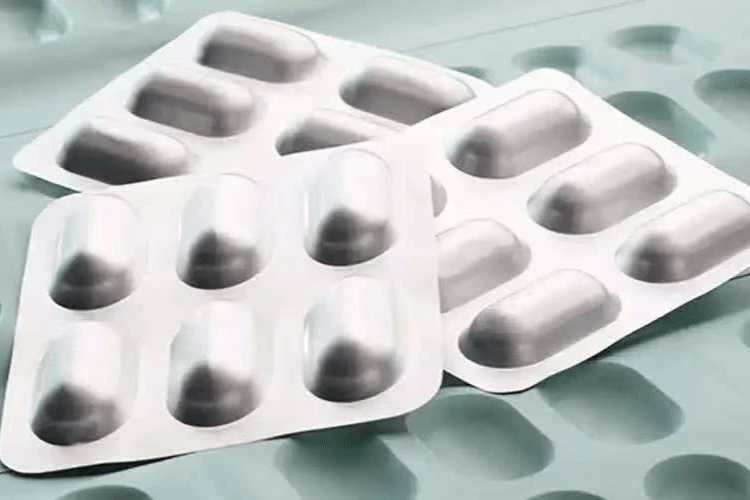
Advantages of Water Born Aluminum Foil Adhesive
Water born aluminum foil adhesive stands out for its eco-friendly properties, making it a sustainable choice in today's environmentally conscious market. This type of adhesive often boasts low volatile organic compounds (VOCs), which not only benefits the environment but also improves workplace safety during application. Additionally, water born adhesives provide excellent adhesion to various substrates, ensuring a strong bond when bonding aluminum in diverse packaging solutions like PTP blister packaging.
Another significant advantage is their ease of clean-up; water-based formulations are typically easier to handle compared to solvent-based options. This convenience can lead to reduced downtime during production processes, allowing for greater efficiency overall. With their versatility and effectiveness, water born laminating adhesives have become increasingly popular among manufacturers looking for reliable bonding solutions without compromising on sustainability.
Limitations of Aluminum Glue Welds
While aluminum glue welds may seem like a quick fix for certain applications, they do come with notable limitations that should be considered before use. One major drawback is that glue welds may not achieve the same level of strength as traditional mechanical fastening methods or high-quality aluminum bonding adhesives. This can lead to concerns about long-term durability and performance under stress or extreme conditions.
Moreover, the curing process for glue welds can be time-consuming and may require specific environmental conditions to achieve optimal results. If not managed properly, this could hinder production timelines and create inefficiencies in manufacturing workflows. Therefore, while they might be suitable for some temporary applications or light-duty tasks, relying solely on aluminum glue welds could compromise overall product integrity.
Evaluating Cost vs Performance
When choosing the best glue for bonding aluminium, evaluating cost versus performance is critical in determining which adhesive will meet your needs effectively without breaking the bank. Water born adhesives typically have a higher upfront cost than traditional solvent-based options; however, their long-term benefits—such as lower VOC emissions and reduced cleanup time—can make them more economical over time when considering operational efficiencies.
On the other hand, while cheaper alternatives may initially seem appealing due to lower prices per unit volume, they might require more frequent reapplications or lead to higher failure rates during use—ultimately costing more in repairs or replacements down the line. To navigate this balancing act successfully requires careful consideration of specific project requirements alongside budget constraints so that you don’t end up with an expensive lesson learned later on.
How to Test Adhesive Performance
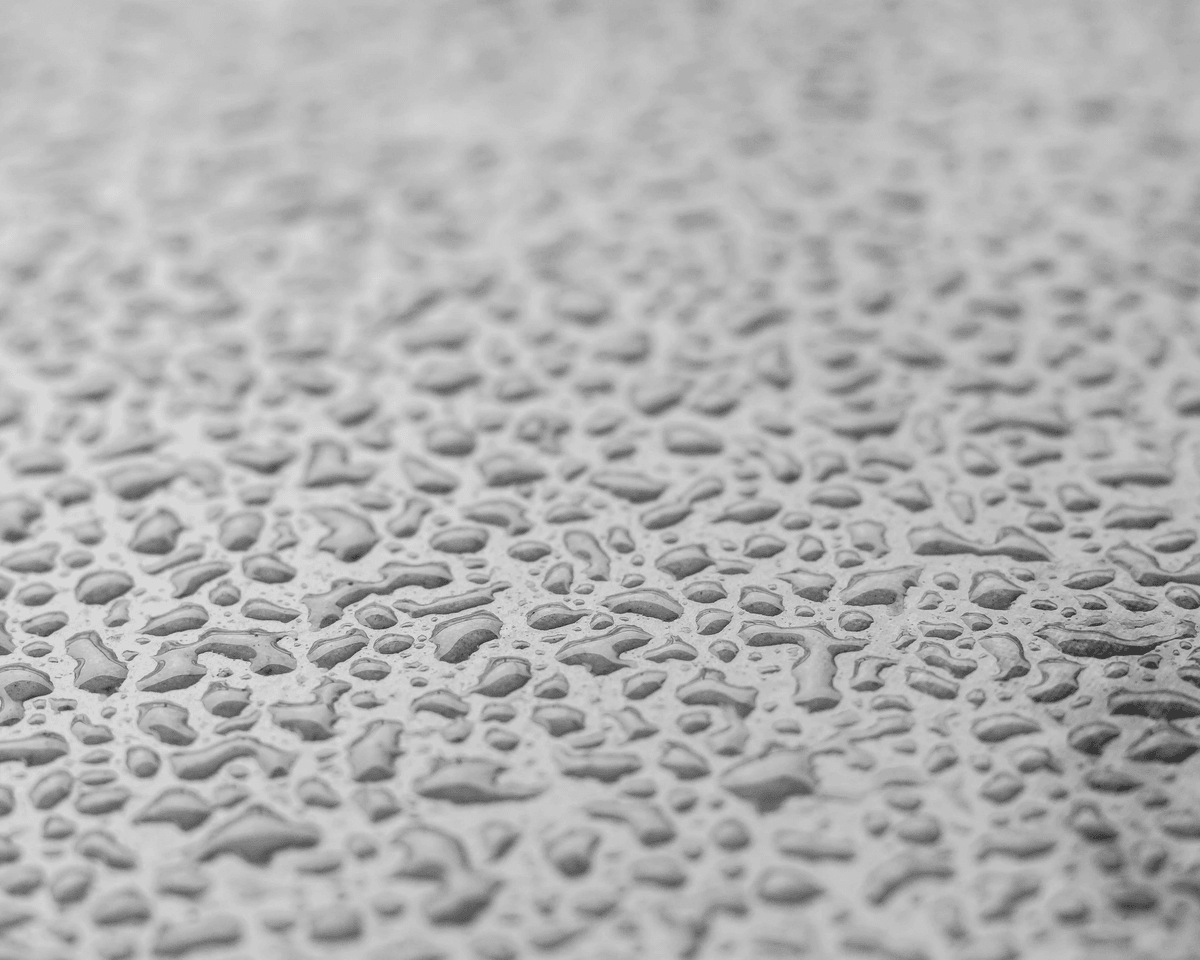
Testing the performance of aluminum bonding adhesives is crucial for ensuring that they meet the demands of various applications. Understanding how well an adhesive performs can save time, money, and headaches down the line. In this section, we will explore several methods for assessing adhesive performance, focusing on bond strength, durability over time, and resistance to environmental factors.
Adhesive Bond Strength Assessment Techniques
One of the most critical aspects of evaluating aluminum bonding adhesives is assessing their bond strength. Techniques such as peel tests and shear tests are commonly used to determine how well an adhesive holds up under stress. For example, a peel test can reveal how effectively water born aluminum foil adhesive adheres to aluminum surfaces by measuring the force required to separate them.
Another effective method involves tensile testing, where samples are pulled apart until failure occurs. This technique helps in selecting the best glue for bonding aluminium by providing quantitative data on maximum load capacities. By understanding these metrics, manufacturers can confidently choose aluminum adhesive sheets that will perform reliably in their specific applications.
Long-Term Durability Testing
Long-term durability testing is essential for understanding how aluminum bonding adhesives hold up over time under various conditions. This process often involves subjecting bonded samples to accelerated aging tests that simulate years of wear and tear in a shorter timeframe. Such evaluations help identify any potential degradation in performance or adhesion loss that might occur with products like water born laminating adhesive.
It's also important to consider real-world scenarios during long-term testing; this means exposing samples to fluctuations in temperature and humidity levels typical for their intended environment. By observing how well these adhesives maintain their integrity over extended periods, manufacturers can make informed decisions about which products are best suited for enduring challenges like those faced in PTP blister packaging applications.
Environmental Resistance Evaluations
Environmental resistance evaluations focus on how well aluminum bonding adhesives withstand exposure to various external factors such as moisture, chemicals, and UV light. For instance, testing a water born adhesive for PTP blister packaging against common solvents or cleaning agents can reveal its suitability for specific uses without compromising bond integrity.
Moreover, it’s essential to assess resistance against temperature extremes—both hot and cold—to ensure that the chosen aluminum glue welds perform under all conditions they might encounter during storage or usage. By conducting thorough environmental evaluations, manufacturers not only guarantee product longevity but also enhance customer satisfaction through reliable packaging solutions.
Conclusion
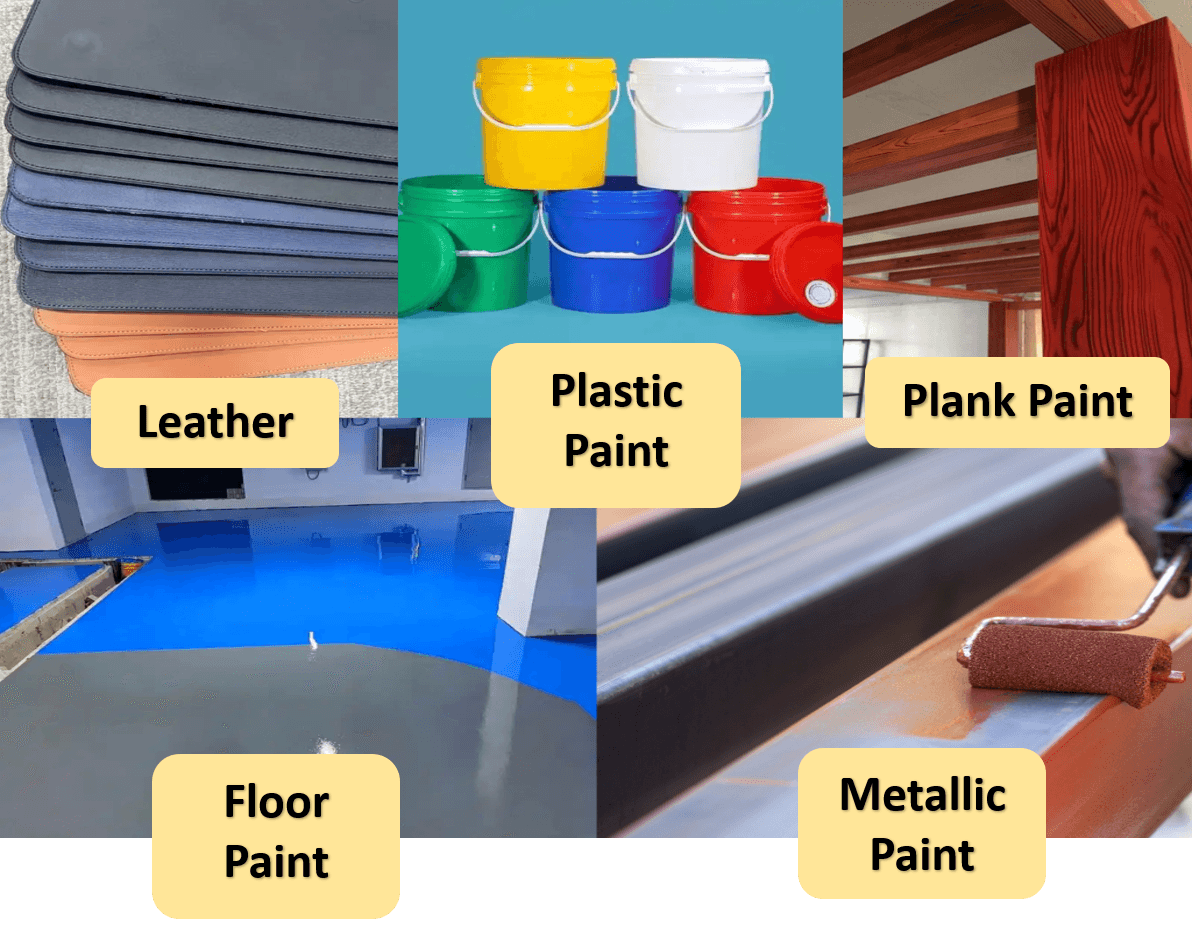
In the world of packaging and industrial applications, choosing the right aluminum bonding adhesive is crucial for achieving strong, lasting bonds. With various options available, from water born aluminum foil adhesive to traditional solvent-based solutions, it’s essential to evaluate your specific needs before making a decision. By understanding the properties of different adhesives and their suitability for bonding aluminum, you can ensure optimal performance in your projects.
Choosing the Best Glue for Bonding Aluminium
Water born adhesives offer sustainable choices without compromising on strength, making them ideal for applications like PTP blister packaging and laminating processes. Meanwhile, traditional aluminum glue welds may still hold value in certain industrial contexts but often come with limitations that should be carefully assessed.
Key Takeaways for Effective Packaging Solutions
Effective packaging solutions hinge on selecting the appropriate aluminum adhesive sheet that meets both performance and environmental standards. Key takeaways include understanding the advantages of water born laminating adhesives versus traditional options and recognizing how each type affects production efficiency. By prioritizing compatibility and testing adhesive performance through bond strength assessments, businesses can enhance their packaging strategies significantly.
Future Trends in Aluminum Bonding Adhesives
Looking ahead, future trends in aluminum bonding adhesives point toward increased innovation in water based formulations that promote sustainability while maintaining high-performance standards. As industries shift towards eco-friendly practices, we can expect to see a rise in demand for water born adhesive solutions tailored specifically for diverse applications like blister packaging or laminating processes. Adapting to these trends will not only benefit manufacturers but also align with consumer preferences for environmentally responsible products.