Introduction
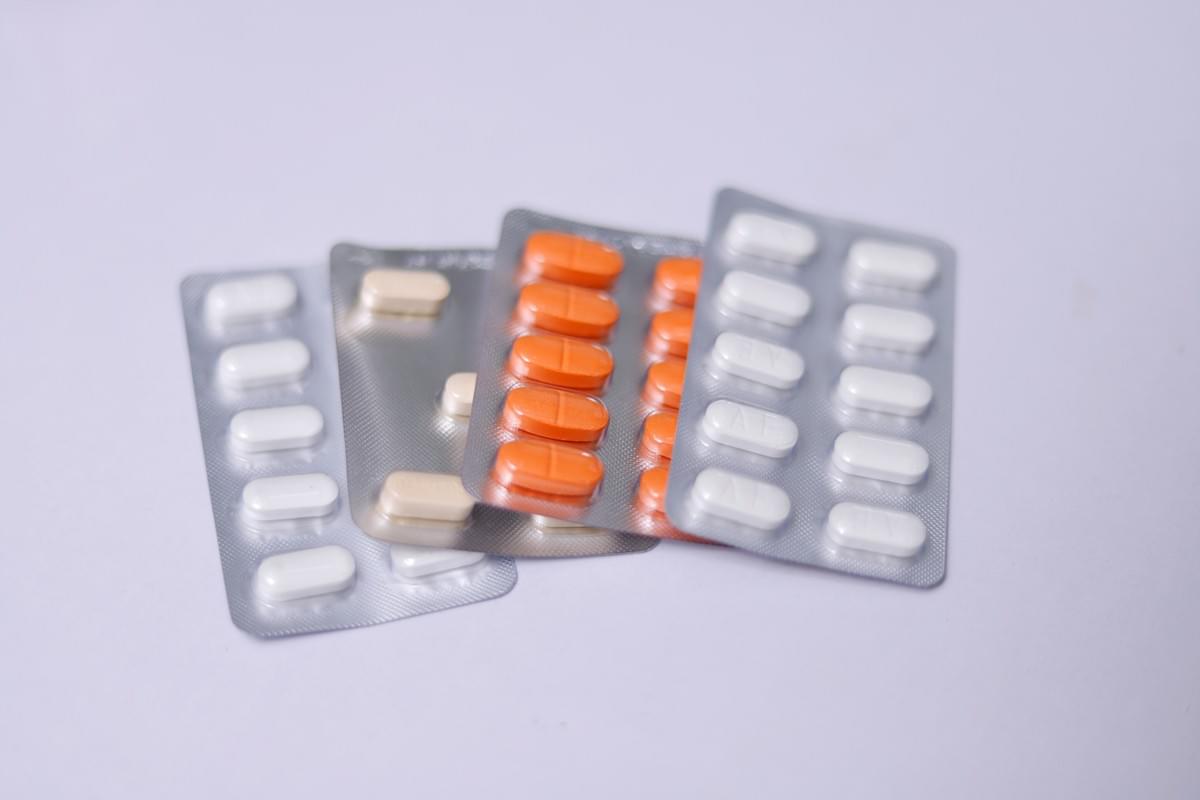
In the world of packaging, aluminum blister adhesive plays a crucial role in ensuring product integrity and consumer safety. These adhesives are not just sticky substances; they are vital components that contribute to the functionality and reliability of blister packs, particularly in medical applications. As we explore the various types of blister pack adhesives, it becomes clear that selecting the right one can make all the difference in maintaining product quality.
The Importance of Aluminum Blister Adhesive
Aluminum blister adhesive is essential for creating secure seals that protect sensitive products from moisture, light, and contamination. This is especially important in industries like pharmaceuticals, where ensuring that medications remain uncontaminated is paramount. Understanding which adhesives are used to make blisters for medical applications can help manufacturers choose the best options for their specific needs.
Exploring Blister Pack Adhesives
Blister pack adhesives come in various formulations designed to meet different performance criteria and application requirements. From flexible packaging adhesives that allow for versatility to specialized laminating adhesives used for enhanced barrier properties, there’s no shortage of choices available on the market today. By exploring these different types of blister pack adhesives, manufacturers can better understand how each option affects product protection and shelf life.
Key Tips for Strong Adhesive Bonds
Achieving strong adhesive bonds requires careful attention to detail during application processes. Factors such as surface preparation techniques, optimal temperature, and humidity conditions play a significant role in determining bond strength and durability. By following key tips tailored to aluminum blister adhesive applications, manufacturers can enhance their packaging's effectiveness while minimizing potential issues down the line.
[Image description=various types of aluminum blister packs displayed on a table with visible labels indicating contents, close-up view highlighting shiny surfaces and sealed edges, background blurred], Image name=aluminum_blister_packs_displayed, Alt tag=Aluminum blister adhesive used in various medical packaging solutions
Understanding Aluminum Blister Adhesive
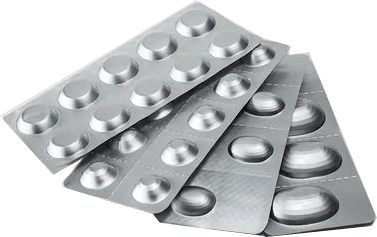
Composition and Properties
The composition of aluminum blister adhesive typically includes polymers such as polyvinyl acetate (PVA), ethylene-vinyl acetate (EVA), or MMA (methyl methacrylate) resins, which contribute to its exceptional bonding capabilities. These adhesives are formulated to provide not only adhesion but also flexibility, durability, and resistance to moisture—qualities essential for maintaining product integrity in flexible packaging. Moreover, their unique properties enable them to withstand temperature variations and mechanical stress during handling and transportation.
Applications in Flexible Packaging
Aluminum blister adhesives are widely used in flexible packaging applications due to their ability to create airtight seals that protect sensitive products like medications from moisture and light exposure. In medical applications specifically, these adhesives ensure that blisters securely contain pills or capsules while allowing for easy access by consumers. Additionally, they can be employed in various other sectors such as food packaging or electronics, demonstrating their versatility as effective laminating adhesives.
Popular Brands and Products
When it comes to aluminum blister adhesives, several popular brands have established themselves as leaders in the market by providing high-quality products tailored for specific needs. Companies like Henkel offer a range of blister pack adhesives designed for both medical and non-medical applications; their commitment to innovation ensures that users can find suitable solutions for various adhesive packaging challenges. Other notable brands include 3M and Dow Chemical Company, which also provide reliable MMA adhesive options that meet industry standards while delivering optimal performance across different applications.
Choosing the Right Adhesive for Your Project
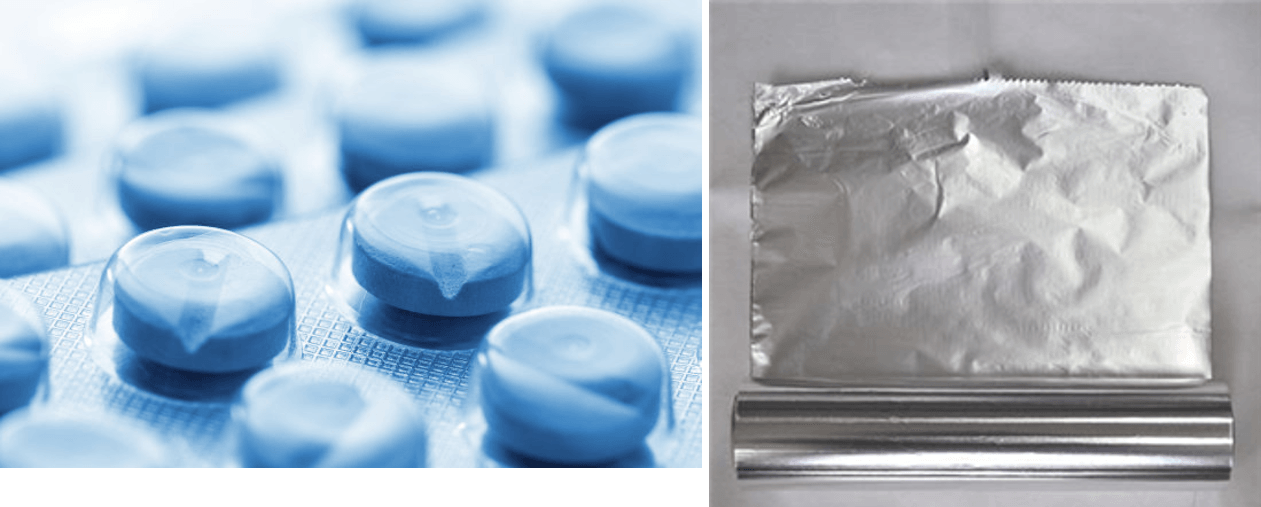
Selecting the right aluminum blister adhesive is crucial for ensuring the integrity and effectiveness of your packaging. With various options available, understanding the specific needs of your project can guide you in making an informed decision. From medical applications to flexible packaging, each adhesive type serves distinct purposes and offers unique benefits.
Which Adhesives Are Used to Make Blisters for Medical Applications?
Common choices include hot melt adhesives, solvent-based adhesives, and specialized aluminum blister adhesives designed for pharmaceuticals. These adhesives must not only provide a strong bond but also be non-toxic and suitable for direct contact with medications.
In addition to safety considerations, these blister pack adhesives often need to withstand various environmental factors such as temperature fluctuations and humidity levels. The selection process may also involve evaluating adhesion strength and peel resistance, ensuring that the medication remains securely packaged until use. Ultimately, choosing the right adhesive is vital in maintaining product integrity while meeting industry standards.
Evaluating MMA Adhesive Options
MMA (Methyl Methacrylate) adhesive options are gaining popularity in the realm of flexible packaging adhesives due to their exceptional bonding capabilities. These adhesives offer impressive resistance against moisture and chemicals, making them ideal for aluminum blister applications where durability is paramount. When evaluating MMA adhesive options, consider factors such as cure time, viscosity, and compatibility with different substrate materials.
One significant advantage of MMA adhesives is their ability to form strong bonds even under challenging conditions—think extreme temperatures or high humidity environments! This makes them a go-to choice for many manufacturers seeking reliable laminating adhesives that won’t falter over time or exposure to external elements. As you explore various MMA options, keep an eye on performance characteristics that align with your specific project requirements.
Factors to Consider for Adhesive Packaging
Choosing an aluminum blister adhesive involves more than just picking a product off the shelf; it's about understanding how it fits into your overall packaging strategy. Key factors include adhesion strength needed based on product weight and material composition of both substrates being bonded together—this will influence whether you opt for hot melts or solvent-based solutions among other flexible packaging adhesives available in the market.
Moreover, consider regulatory compliance if you're working within sectors such as pharmaceuticals or food products; this will dictate not only which types of adhesive you can use but also how they should be applied during manufacturing processes. Additionally, evaluate cost-effectiveness without compromising quality; after all, strong bonds shouldn’t break the bank!
Tips for Proper Application
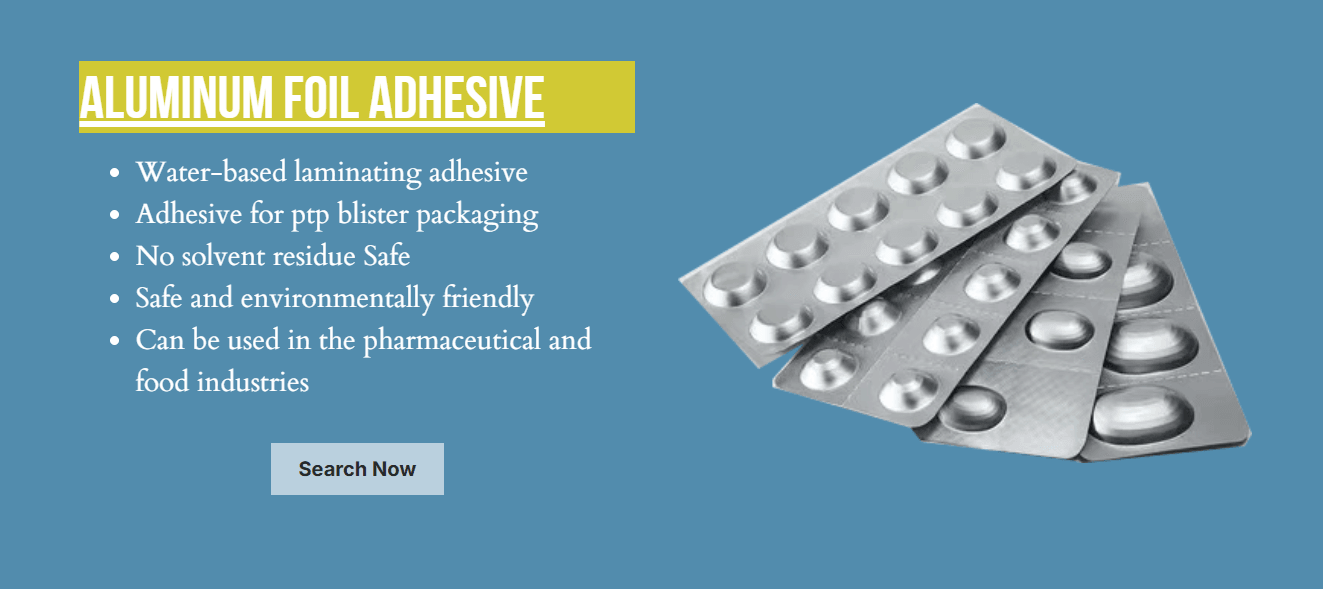
Surface Preparation Techniques
Surface preparation is the unsung hero in the world of aluminum blister adhesives. Before applying any adhesive, ensure that the surfaces are clean and free from dust, grease, or moisture—these contaminants can sabotage even the best adhesive formulations. For optimal results, consider using appropriate solvents or cleaners specifically designed for flexible packaging adhesives to enhance adhesion and ensure a smooth bonding process.
In addition to cleaning, roughening up the surface can also help improve adhesion by increasing the area for bonding. Using abrasives or sandpaper on aluminum surfaces may create micro-textures that allow for better mechanical interlocking with your chosen laminating adhesives. Remember, a little prep work goes a long way in ensuring that your medical applications stand up to rigorous use.
Optimal Temperature and Humidity Conditions
The environment plays a significant role in how aluminum blister adhesive performs during application and curing phases. Ideally, aim for temperatures between 20°C to 25°C (68°F to 77°F) with relative humidity levels below 60%. High humidity can lead to moisture infiltration which compromises bond strength; therefore, monitoring these conditions is vital when working with blister pack adhesives.
If working in less-than-ideal conditions is unavoidable, consider adjusting your application process accordingly—this may include extending curing times or using heat-assisted methods where feasible. Additionally, ensure that materials are acclimatized to room temperature before application; this helps prevent thermal shock which could weaken bonds formed by MMA adhesives or other types of flexible packaging adhesives.
Effective Bonding Methods
Choosing the right bonding method is essential for maximizing the effectiveness of aluminum blister adhesive in your projects. Common techniques include roller coating, spray application, or brush application depending on project scale and complexity; each method offers unique advantages when it comes to coverage and control over adhesive thickness. When dealing with medical applications specifically, precision is key—ensure uniform coverage without excess pooling of adhesive.
For larger production runs involving blister packs or complex shapes requiring more intricate designs, automated systems may be beneficial as they provide consistency across multiple items while reducing labor costs associated with manual methods. Regardless of technique used, always follow manufacturer guidelines regarding cure times and pressure settings post-application; this ensures optimal bond strength is achieved before products hit shelves.
Chemix's Water-Based Resin Solution
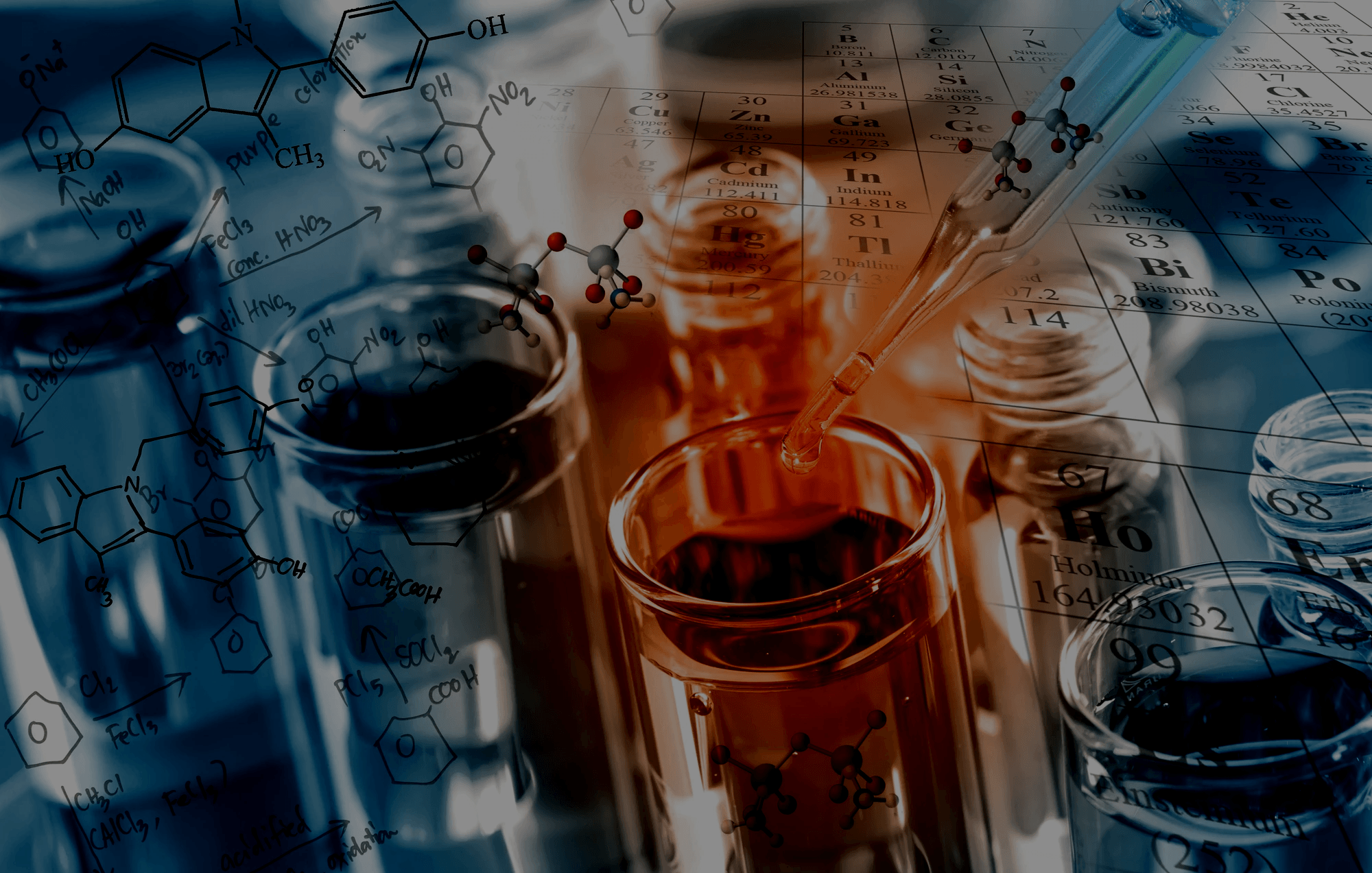
In the realm of aluminum blister adhesive, Chemix’s water-based resin solution stands out as a sustainable alternative that addresses both performance and environmental concerns. With an increasing push for eco-friendly materials in various industries, these adhesives offer a way to achieve strong bonds without compromising on safety or quality. By choosing water-based options, manufacturers can align their products with modern sustainability goals while maintaining the effectiveness required for applications like blister packaging.
Advantages of Sustainable Adhesives
Sustainable adhesives, particularly those that are water-based, come with a plethora of advantages that make them appealing for flexible packaging adhesives. First and foremost, they contain fewer volatile organic compounds (VOCs), which means they contribute less to air pollution and are safer for workers during application. Additionally, using sustainable aluminum blister adhesive helps companies meet regulatory requirements while appealing to environmentally conscious consumers who prioritize green products.
Moreover, Chemix’s water-based resin solutions provide excellent adhesion properties comparable to traditional MMA adhesive options but with added benefits such as easier cleanup and reduced flammability risks. This makes them ideal for various applications beyond just blister packs—think laminating adhesives used in food packaging or other sensitive products where safety is paramount. Ultimately, opting for sustainable solutions not only enhances product appeal but also demonstrates corporate responsibility.
How Water-Based Resin Performs
These resins exhibit excellent adhesion to diverse substrates commonly used in flexible packaging—ensuring that your product stays securely sealed until it's ready to be opened by consumers. Plus, their versatility allows them to perform well under varying conditions such as temperature fluctuations and humidity levels.
One standout feature of these adhesives is their improved flexibility compared to traditional counterparts; this characteristic is crucial when dealing with complex shapes often found in medical blisters or intricate designs in consumer goods packaging. The result? A strong bond that withstands stress without compromising the integrity of the package itself—a significant advantage when considering which adhesives are used to make blisters for medical applications!
Additionally, water-based resins facilitate faster drying times than many solvent-based products—meaning quicker production cycles and more efficient workflows for manufacturers relying on adhesive packaging solutions.
Ideal Uses in Aluminum Blister Applications
Chemix's water-based resin solution is perfectly suited for various aluminum blister applications due to its unique properties and performance advantages over traditional options like MMA adhesive formulations. In particular, it shines brightly in the pharmaceutical sector where strict compliance with safety standards is non-negotiable; using these resins ensures that blisters remain intact while safeguarding sensitive contents from moisture or contamination.
Furthermore, these versatile adhesives can be employed across a range of industries beyond pharmaceuticals—think cosmetics or electronics where protective packaging plays a vital role in preserving product quality during transport and storage! Their adaptability makes them an ideal choice not only for aluminum blister packs but also as laminating adhesives within multi-layered structures designed for enhanced durability.
In conclusion, when considering flexible packaging adhesives specifically tailored for aluminum blisters, Chemix's innovative water-based resins emerge as champions—not just because they’re sustainable but also due to their exceptional performance across numerous applications.
Troubleshooting Common Adhesive Issues
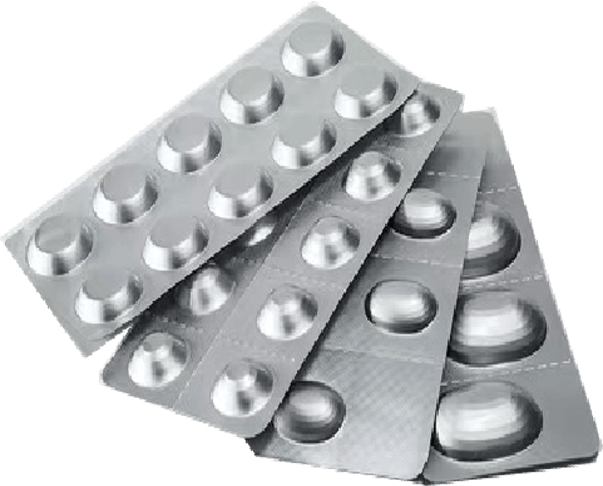
When working with aluminum blister adhesive, it’s not uncommon to encounter a few hiccups along the way. Understanding the common issues that can arise during the bonding process is essential for ensuring high-quality results in flexible packaging. This section dives into how to identify bond failures, offers solutions for weak adhesive bonds, and provides preventive measures to keep your projects running smoothly.
Identifying Bond Failure Causes
Bond failure can result from various factors, making it crucial to diagnose the underlying issue accurately. One of the primary culprits in aluminum blister adhesive applications is inadequate surface preparation, which may leave contaminants that hinder adhesion. Additionally, environmental conditions such as temperature and humidity can significantly affect how well blister pack adhesives perform; if they’re not optimal, you might find yourself with weak bonds.
Another common cause of bond failure relates to the choice of adhesive itself. For instance, if you're wondering which adhesives are used to make blisters for medical applications, be aware that not all adhesives are created equal; using an inappropriate type may lead to performance issues. Lastly, improper curing or drying times can also contribute to bond weaknesses—something that often gets overlooked in fast-paced production environments.
Solutions for Weak Adhesive Bonds
Once you've identified the causes of weak adhesive bonds in your aluminum blister packaging project, it's time to take action. First and foremost, revisiting your surface preparation techniques is essential; ensure surfaces are clean and free from oils or dust before applying any flexible packaging adhesives. You might also consider switching to a more suitable MMA adhesive known for its strong bonding capabilities if you suspect your current choice isn’t cutting it.
If environmental conditions are at play—such as too much humidity—adjusting these factors can make a world of difference. Implementing climate control measures in your workspace will help maintain ideal temperatures and humidity levels conducive to effective adhesion. Additionally, reviewing application methods and ensuring proper curing times can enhance overall bond strength significantly.
Preventive Measures for Future Projects
To avoid encountering similar issues down the road with aluminum blister adhesive applications, proactive planning is key! Start by investing time in selecting the right laminating adhesives tailored specifically for your project requirements; this will set a solid foundation right from the get-go. Training staff on proper application techniques also goes a long way—knowledge sharing ensures everyone understands best practices when working with blister pack adhesives.
Regularly reviewing equipment maintenance schedules helps prevent mechanical failures that could impact adhesion quality as well; keeping machines running smoothly is just as important as choosing the right materials! Finally, establishing a robust quality control process allows you to catch potential problems early on before they escalate into larger issues during production runs.
Conclusion
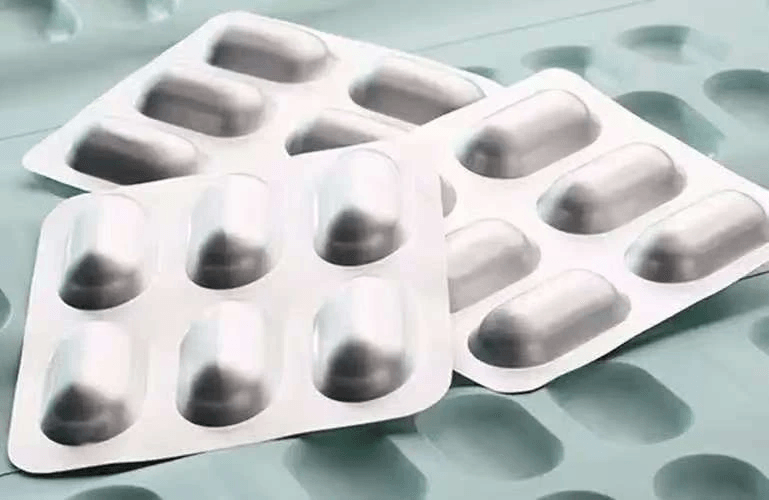
In the world of packaging, aluminum blister adhesive stands out for its versatility and effectiveness. These adhesives play a crucial role in creating secure and reliable blister packs that protect products, especially in the medical field. With advancements in technology and a growing emphasis on sustainability, the future looks bright for these essential materials.
Recap of Aluminum Blister Adhesive Benefits
Aluminum blister adhesive brings numerous benefits to both manufacturers and consumers alike. Its strong bonding capabilities ensure that products remain safe from external elements while maintaining freshness, particularly important in medical applications where safety is paramount. Moreover, the use of flexible packaging adhesives allows for lightweight designs without compromising durability or performance.
Future Trends in Adhesive Technologies
Looking ahead, we can expect exciting developments in adhesive technologies that will further enhance aluminum blister adhesive applications. Innovations such as bio-based adhesives and improved MMA adhesive formulations are on the horizon, promising better performance with less environmental impact. Additionally, as industries continue to prioritize sustainability, laminating adhesives that are eco-friendly will likely gain traction, reshaping the landscape of adhesive packaging.
Final Thoughts on Strong Bonds
In conclusion, strong bonds formed by aluminum blister adhesives are not just about holding materials together; they symbolize reliability and innovation in packaging solutions. As we navigate through evolving trends and technologies, it’s essential to stay informed about which adhesives are used to make blisters for medical applications and how they can be optimized for various uses. Ultimately, investing in quality materials today will pave the way for safer products tomorrow.