Introduction
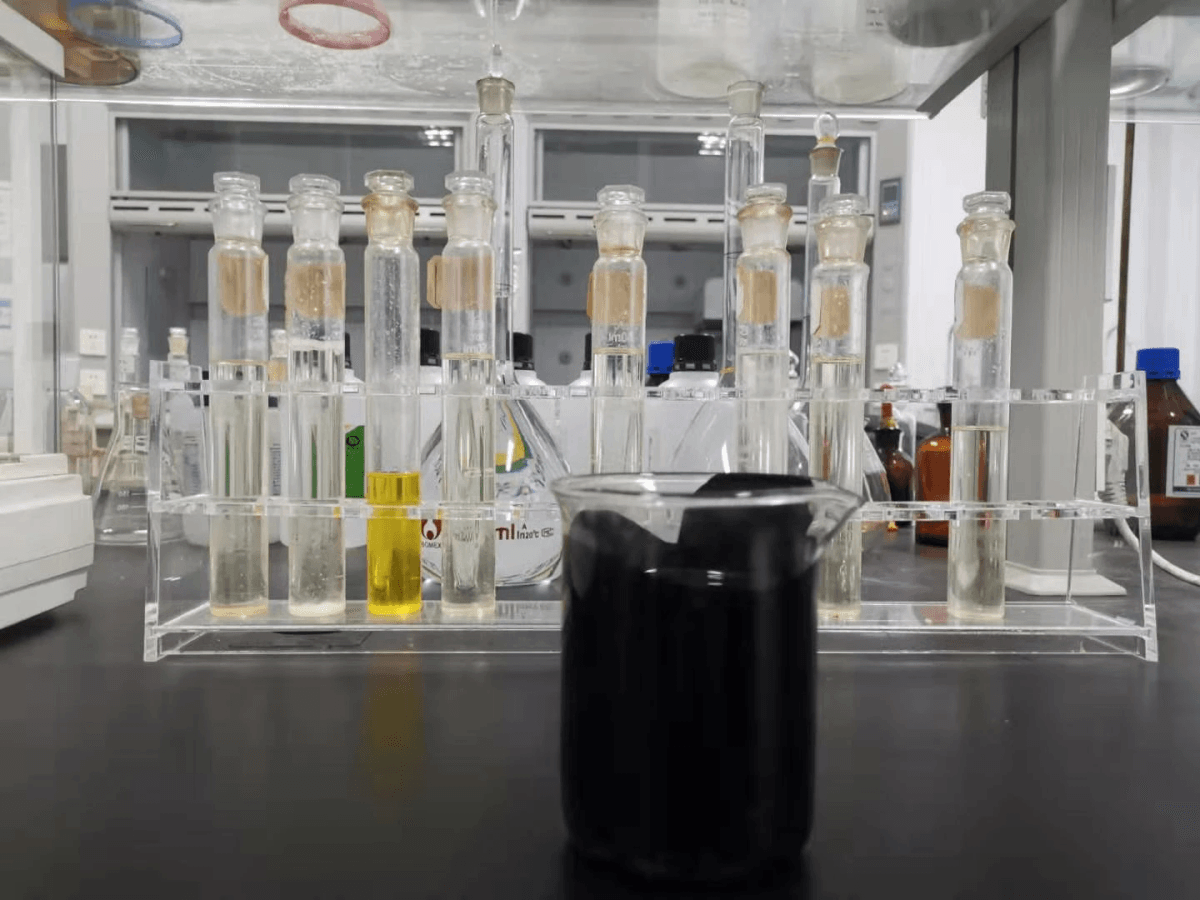
In the realm of medical packaging, blister packs are vital for ensuring the integrity and safety of pharmaceuticals. Understanding blister medical pack needs is crucial for manufacturers, as these packages must protect sensitive products from environmental factors while allowing for easy access by end-users. Selecting the right materials, particularly medical adhesives, plays a significant role in achieving these objectives.
Understanding Blister Medical Pack Needs
Blister packs serve not only as a protective barrier but also as a means to organize and dispense medications efficiently. They need to be durable enough to withstand transportation and handling while remaining user-friendly for patients who may have varying degrees of dexterity. The choice of adhesive is pivotal; it must securely bond different layers without compromising the product inside, making it essential to explore the best adhesives for blister packaging.
Key Factors for Selecting Adhesives
When selecting adhesives for blister pack applications, several key factors come into play: adhesion strength, compatibility with materials, and environmental impact. A strong bond is essential to ensure that the blister pack remains intact throughout its lifecycle—from manufacturing to use—while material compatibility prevents any adverse reactions that could affect product quality. Additionally, considering eco-friendly options aligns with growing sustainability trends in medical packaging.
The Role of Medical Adhesives
Medical adhesives are not just simple bonding agents; they serve a critical function in maintaining product integrity and safety within blister packs. They help ensure that medications remain sealed until use, reducing contamination risks and enhancing shelf life. Moreover, as innovation continues in adhesive technology, new formulations are emerging that prioritize both performance and environmental responsibility—making them indispensable in modern blister packaging solutions.
Types of Medical Adhesives
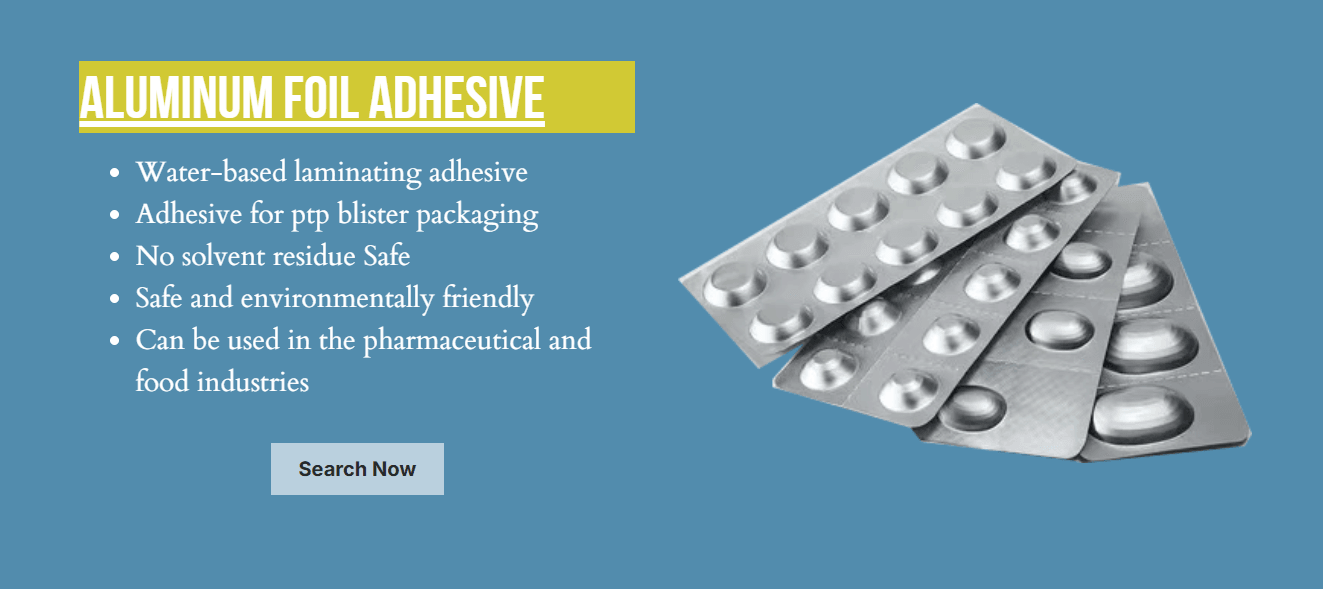
Overview of Common Medical Adhesives
Medical adhesives come in several varieties, including pressure-sensitive adhesives (PSAs), hot melt adhesives, and water-based adhesives. PSAs are popular due to their ease of use and quick bonding capabilities; they adhere well to skin and other surfaces without requiring heat or special conditions. Hot melt adhesives offer strong bonds but may not always be suitable for sensitive applications, while water-based adhesives are gaining traction for their eco-friendliness and versatility in various settings.
Water-Based Adhesives Explained
Water-based adhesives have emerged as a preferred choice in many medical applications due to their environmentally friendly composition and lower toxicity levels compared to solvent-based options. These adhesives utilize water as a solvent, allowing them to bond effectively while minimizing harmful emissions during production and application. Their formulation makes them ideal for sensitive environments like hospitals or clinics where patient safety is paramount.
Pros and Cons of Each Type
Each type of medical adhesive has its strengths and weaknesses that can affect performance in blister pack applications. For instance, while PSAs offer immediate adhesion, they may degrade over time when exposed to moisture or temperature fluctuations; thus, they might not be the best choice for all blister pack applications. Conversely, water-based adhesives provide excellent flexibility and safety but may require longer curing times compared to hot melts—making it essential for manufacturers to weigh these factors carefully when choosing the best adhesives for blister packaging.
Best Adhesives for Blister Packaging
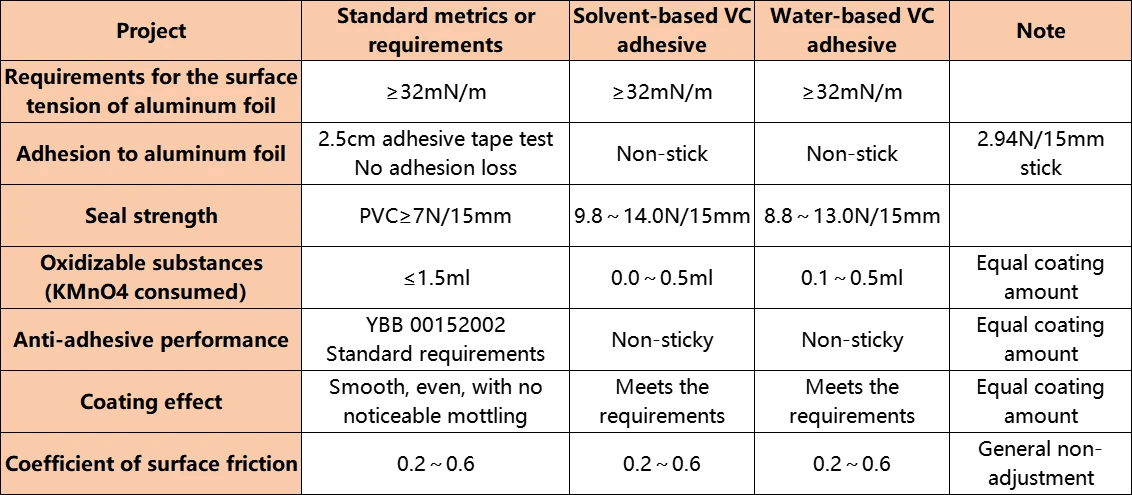
When it comes to selecting the best adhesives for blister packaging, the options can be as varied as the products they hold. Medical adhesive choices need to be reliable, safe, and effective in maintaining product integrity while ensuring user safety. This section will delve into top choices for blister pack adhesives and how they stack up against each other.
Top Choices for Blister Pack Adhesives
In the world of medical adhesive options, several contenders stand out as top choices for blister pack adhesives. First on our list is polyacrylate-based adhesives, known for their strong bonding capabilities and versatility across various substrates. Next up are water-based adhesives, which are gaining popularity due to their eco-friendliness and lower VOC emissions—an excellent choice for manufacturers looking to enhance sustainability in their packaging solutions.
Another noteworthy option is hot melt adhesives; these are particularly favored in high-speed production environments due to their quick setting times and robust adhesion properties. Silicone-based adhesives also deserve a mention, especially when flexibility and skin compatibility are paramount. Each of these medical adhesive types has its unique advantages that cater to specific needs within blister packaging.
Performance Comparisons of Leading Brands
When evaluating the best adhesives for blister packaging, it’s crucial to compare leading brands on performance metrics such as adhesion strength, durability under stress, and user safety profiles. For instance, Brand A's polyacrylate adhesive boasts an impressive peel strength that outperforms many competitors but can struggle with moisture resistance compared to Brand B's water-based solution.
Brand C’s hot melt adhesive shines in rapid production settings but may not offer the same level of flexibility as silicone alternatives from Brand D. Ultimately, the decision often boils down to balancing performance characteristics with specific application requirements—whether that be speed of production or environmental considerations.
Real-World Applications
Real-world applications of these best adhesives for blister packaging illustrate how critical the right choice can be in a clinical setting. For example, polyacrylate-based medical adhesives are frequently used in surgical dressings due to their strong bond yet gentle removal properties on sensitive skin surfaces. Meanwhile, water-based adhesives find their niche in environmentally conscious companies aiming to reduce their carbon footprint without compromising product integrity.
Hot melt adhesives often dominate high-volume pharmaceutical operations where speed is essential; however, they might not always suit delicate applications like wound care products where a softer touch is necessary. Understanding these real-world applications helps manufacturers make informed decisions about which medical adhesive will best serve both their products and end-users alike.
Chemix's Water-Based Resin Solution
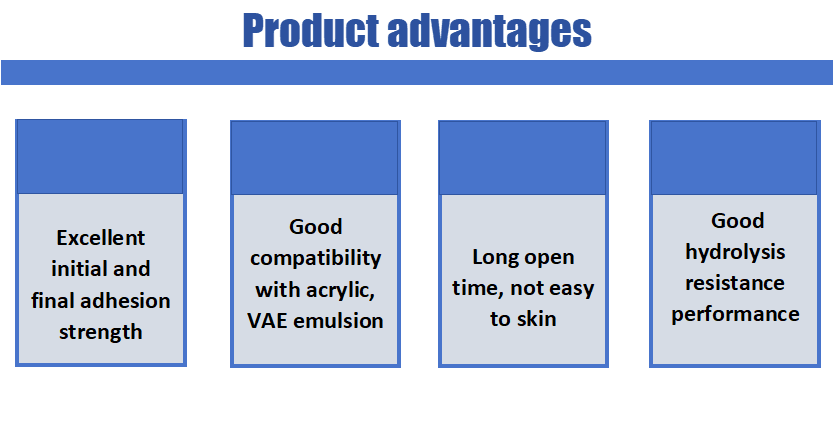
Environmentally Friendly Packaging Options
In today’s world, consumers and manufacturers alike are placing greater emphasis on sustainability, and Chemix’s water-based resin fits the bill perfectly. These environmentally friendly packaging options are designed to minimize ecological impact while maintaining the necessary adhesive properties required for medical applications. By choosing these water-based solutions, companies can significantly reduce their carbon footprint while ensuring that their blister pack adhesives perform reliably.
Advantages of Using Water-Based Resin
Water-based resins offer several advantages over traditional solvent-based adhesives, making them among the best adhesives for blister packaging available today. First and foremost, they are safer for both users and the environment due to lower volatile organic compounds (VOCs). Additionally, these resins provide excellent adhesion properties without sacrificing flexibility or durability—ideal characteristics for medical adhesive applications where reliability is crucial.
Moreover, using water-based resin helps streamline production processes since they often require less equipment cleaning and maintenance compared to solvent-based alternatives. This efficiency can lead to cost savings over time while ensuring that companies adhere to stringent regulatory standards in the medical field. In essence, opting for Chemix's water-based solution means choosing an adhesive that balances performance with responsibility.
Application in Blister Medical Packs
The application of Chemix’s water-based resin in blister medical packs showcases its versatility and effectiveness as a top-tier medical adhesive solution. These resins bond securely with various substrates commonly used in blister packaging, ensuring that medications remain protected from external elements until they are ready for use. The strong adhesion provided by this innovative product ensures that even delicate items remain securely packaged without risk of damage during transit or handling.
Furthermore, the ease of application allows manufacturers to integrate these adhesives seamlessly into existing production lines without significant adjustments or downtime—an essential factor when considering efficiency in manufacturing processes. As more companies recognize the benefits associated with using water-based resin solutions like those offered by Chemix, we can expect a shift towards greener practices within the industry while still delivering high-quality blister pack adhesives.
Adhesive Application Techniques
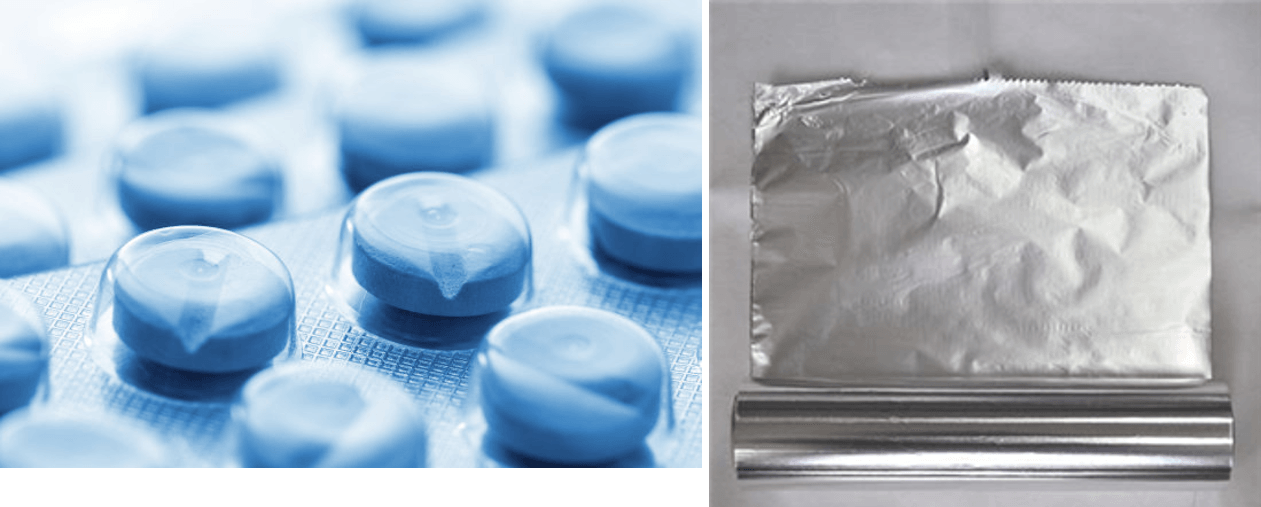
Best Practices for Adhesive Application
To achieve optimal performance with blister pack adhesives, several best practices should be followed. First, ensure that surfaces are clean and dry before application; any contaminants can compromise the bond strength of the medical adhesive. Additionally, applying the adhesive evenly across the surface will create a consistent seal that prevents leakage and maintains sterility.
Another critical practice is to apply pressure after placing your blister pack components together; this helps activate the adhesive's full bonding potential. Timing also plays an essential role—adhesives often have specific working times before they set, so it's crucial to adhere to these guidelines for maximum effectiveness. Lastly, always test your application method on sample packs before full-scale production to identify any potential issues early on.
Equipment and Tools for Precision
Using the right equipment can elevate your application process from good to great when dealing with blister pack adhesives. Automated dispensing systems are highly recommended for achieving consistent bead sizes and even coverage of medical adhesive across various surfaces. These systems can be programmed for speed and pressure, ensuring uniformity in every batch produced.
Moreover, consider using specialized rollers or applicators designed specifically for medical adhesives; these tools help distribute pressure evenly while minimizing waste. For smaller operations or manual applications, precision syringes or brushes can offer control over adhesive placement without sacrificing quality. Investing in proper equipment not only improves efficiency but also enhances product reliability.
Common Mistakes to Avoid
Even seasoned professionals can fall prey to common pitfalls when applying medical adhesives in blister packaging—being aware of these traps is half the battle won! One major mistake is over-applying adhesive; too much can lead to oozing or insufficient bonding strength due to improper curing conditions. Always follow manufacturer recommendations regarding application thickness.
Another frequent error involves neglecting environmental factors such as temperature and humidity during application; both play significant roles in how well your blister pack adhesives perform over time. Failing to account for these variables may result in compromised seals that could jeopardize product safety or efficacy later on. Lastly, don’t skip quality checks post-application—routine inspections help catch any mistakes early before they escalate into costly recalls.
Quality Control in Blister Packing
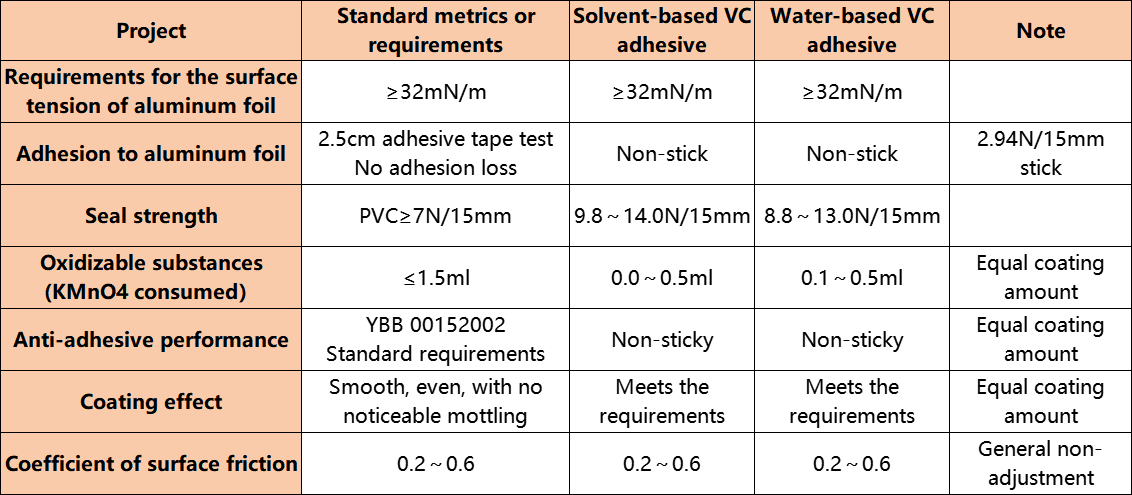
Quality control is the unsung hero of blister packaging, particularly when it comes to medical adhesives. Ensuring that the adhesive used in blister packs meets stringent performance standards is crucial for patient safety and product efficacy. A robust quality control process can help identify potential issues before they escalate, safeguarding both manufacturers and consumers alike.
Importance of Testing Adhesive Strength
Testing adhesive strength is paramount in the realm of medical adhesives, especially for those used in blister pack applications. Strong adhesion ensures that the packaging remains intact during transport and storage, protecting sensitive contents from contamination or damage. Regular testing can reveal variations in adhesive performance, allowing manufacturers to select the best adhesives for blister packaging that meet their specific needs.
Regulatory Standards to Consider
In the world of medical packaging, adhering to regulatory standards is non-negotiable. Organizations like the FDA set forth guidelines that dictate how medical adhesives should perform within blister packs—ensuring they are safe and effective for end-users. Staying compliant not only helps avoid costly recalls but also builds trust with healthcare providers and patients who rely on these products.
Maintaining Consistency in Production
Consistency is key when it comes to using blister pack adhesives effectively across various production runs. Variability can lead to compromised product integrity, which is why implementing strict protocols during manufacturing is essential. Regular audits and calibration of equipment used for applying medical adhesives will ensure that every batch meets quality benchmarks—making your products a reliable choice in a competitive market.
Conclusion
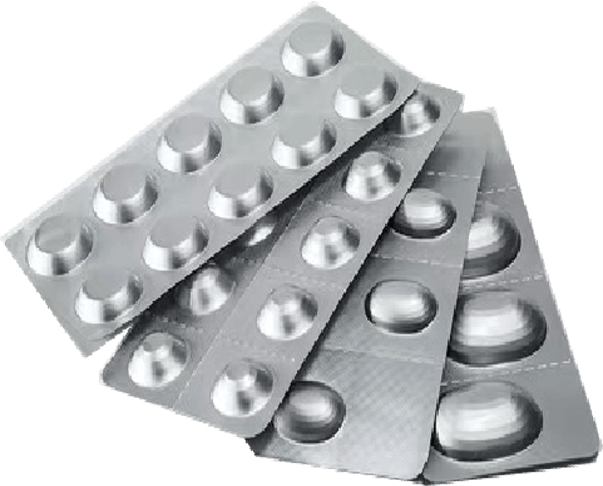
As we wrap up our exploration of blister packaging and the crucial role of medical adhesives, it becomes clear that choosing the right adhesive is a vital step in ensuring product safety and efficacy. With numerous options available, including water-based solutions and various brands, decision-makers must weigh factors such as adhesion strength, environmental impact, and application techniques. Ultimately, the right choice in medical adhesive can enhance product integrity while meeting regulatory standards.
Choosing the Right Medical Adhesive
When selecting from the best adhesives for blister packaging, it's essential to consider specific application needs and end-user safety. Factors such as moisture resistance, shelf life, and compatibility with different substrates should guide your choices. By understanding these elements thoroughly, manufacturers can ensure that their products remain secure while providing optimal performance with their chosen medical adhesive.
Future Trends in Blister Packaging
The future of blister packaging is poised for exciting advancements driven by technology and consumer demand for safer products. Innovations such as smart blister packs that monitor medication adherence or incorporate tamper-evident features are on the horizon. As these trends develop, they will undoubtedly influence the selection of blister pack adhesives to ensure compatibility with new materials and functionalities.
Enhancing Sustainability in Medical Packaging
Sustainability is no longer just a buzzword; it’s becoming a necessity in medical packaging solutions. The shift towards eco-friendly materials like water-based adhesives reflects a growing commitment to reducing environmental impact without compromising quality or safety standards. By prioritizing sustainable practices when choosing blister pack adhesives, manufacturers can contribute to a healthier planet while still delivering reliable products.