Introduction
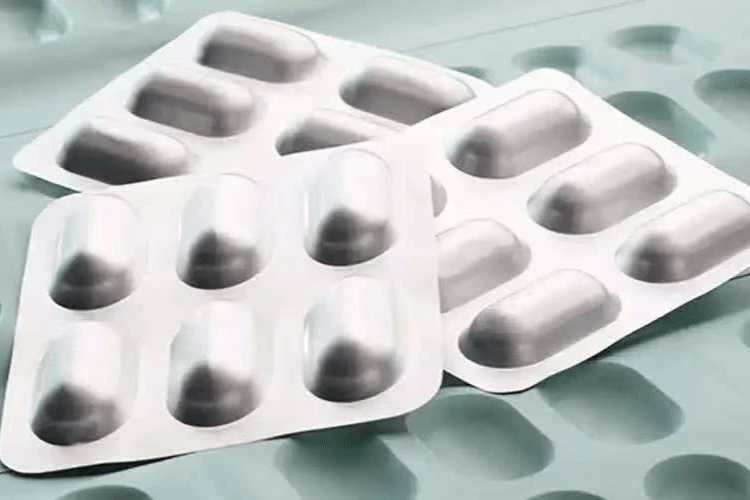
Blister packaging has become a cornerstone in the pharmaceutical and consumer goods industries, ensuring product integrity and safety during transportation and storage. This packaging method not only protects items from environmental factors but also provides an easy-to-use interface for consumers. The effectiveness of blister packs largely hinges on the quality of the adhesives used, making their selection critical for optimal performance.
Overview of Blister Packaging Importance
Blister packaging is essential for preserving the efficacy and safety of medical products, particularly in pharmaceuticals where contamination can lead to serious health risks. The transparent nature of blister packs allows consumers to easily see what they are purchasing while providing a robust barrier against moisture, light, and air that could compromise product quality. In this context, understanding the nuances of adhesive for aluminum blister applications becomes paramount to ensure that packages remain sealed until they reach the end user.
Role of Adhesives in Medical Applications
Adhesives play a pivotal role in medical applications by securing blister packs tightly to prevent leakage or contamination. The right adhesive not only ensures that products remain sterile but also withstands various environmental conditions throughout their lifecycle. Questions like What is the best adhesive for aluminum? arise frequently among manufacturers looking to enhance their packaging solutions while maintaining compliance with health regulations.
Introduction to Protective Adhesives
Protective adhesives are designed specifically for demanding applications like aluminum blister packaging, where high strength and durability are non-negotiable attributes. These adhesives must adhere firmly yet allow for easy opening without compromising the contents inside—an ideal balance that can be tricky to achieve. As we explore options such as Water-Based Adhesive Liquid Sealant Polyurethane Blister solutions, it’s crucial to identify what constitutes a high-strength adhesive for aluminum that meets both performance and safety standards.
Understanding Protective Adhesives
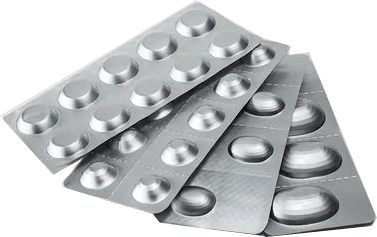
In the realm of blister packaging, protective adhesives play a crucial role, especially when dealing with aluminum materials. These adhesives ensure that products remain securely sealed while providing the necessary protection against environmental factors. Understanding what makes an adhesive effective for aluminum blisters is key to ensuring product integrity and safety.
What is Protective Adhesive for Aluminum?
Protective adhesive for aluminum refers to specialized bonding agents designed to adhere effectively to aluminum surfaces used in blister packs. This type of adhesive is engineered to withstand various conditions, including temperature fluctuations and moisture exposure, which are common in medical applications. When asking, What is the best adhesive for aluminum? it’s essential to consider not just the bond strength but also its compatibility with the materials being sealed.
Advantages of Using Adhesives in Blister Packaging
Using adhesives in blister packaging offers numerous advantages that enhance product safety and usability. First and foremost, they provide a strong seal that prevents contamination and ensures product integrity during storage and transport. Additionally, opting for an adhesive for aluminum blister allows manufacturers to create tamper-evident packaging that increases consumer trust while reducing the risk of product spoilage.
Key Properties of Effective Blister Pack Adhesives
Effective blister pack adhesives must possess several key properties to ensure optimal performance. High strength is critical; therefore, many manufacturers seek out what is a high-strength adhesive for aluminum that can endure stress without compromising seal integrity. Furthermore, these adhesives should exhibit flexibility and resistance to environmental factors such as humidity and temperature changes—qualities often found in options like Water-Based Adhesive Liquid Sealant Polyurethane Blister.
Application of Adhesive for Aluminum Blister
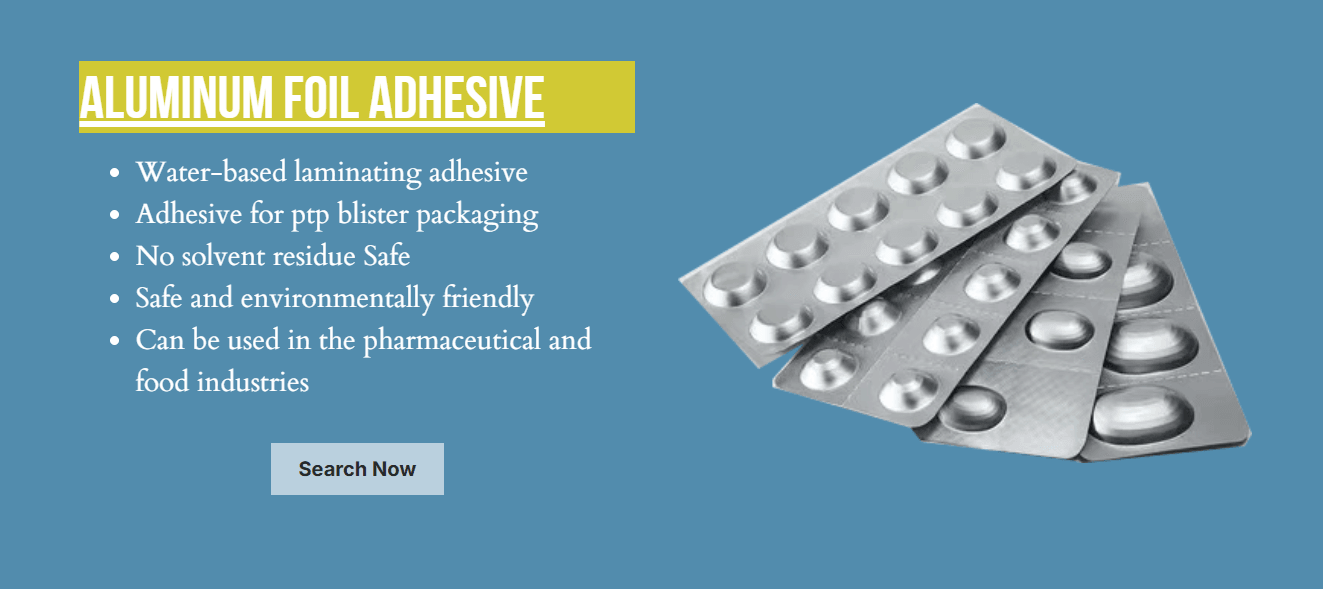
When it comes to sealing aluminum blister packs, the application of the right adhesive is crucial. The choice of adhesive can significantly impact the integrity and safety of the packaged product, especially in medical applications. Understanding how to effectively apply these adhesives ensures that blister packs are both functional and reliable.
Step-by-Step Guide on Sealing Blister Packs
To begin sealing a blister pack, first ensure that all surfaces are clean and dry; this is essential for achieving a strong bond with your chosen adhesive for aluminum blister. Next, apply a uniform layer of adhesive—such as a Water-Based Adhesive Liquid Sealant Polyurethane Blister—on either the aluminum surface or the backing material, depending on your design requirements. Once applied, carefully align the two parts before pressing them together firmly to ensure an even seal; holding them in place for several seconds will help achieve maximum adhesion.
After sealing, it’s important to allow adequate curing time as specified by the adhesive manufacturer; this ensures that you achieve optimal strength and durability in your seal. You may also want to inspect the edges for any gaps or bubbles which could compromise your seal's effectiveness. If everything looks good, you can proceed with packaging or shipping your product confidently!
Factors Influencing Adhesive Choice
Choosing an adhesive for aluminum blisters involves considering several key factors such as compatibility with materials, environmental conditions, and intended use of the package. For instance, if you're working with sensitive medical products, selecting an FDA-approved adhesive would be essential to ensure safety and compliance standards are met. Additionally, understanding what is a high strength adhesive for aluminum will help you determine which products can withstand various stressors during transport or storage.
Another critical factor is whether you need a fast-curing solution versus one that allows more working time; some applications may require quick turnaround times while others might benefit from extended open times for adjustments. Temperature resistance is also vital—certain adhesives perform better under extreme conditions than others—so be sure to check technical specifications before making your selection.
What is the Best Adhesive for Aluminum?
When pondering what is best adhesive for aluminum?, many professionals lean toward specific formulations designed explicitly for blister packaging applications. High-strength adhesives like cyanoacrylate or specialized polyurethane blends often emerge as top contenders due to their exceptional bonding capabilities and versatility across different substrates including wood when necessary.
If you're looking specifically at construction projects involving both wood and aluminum components—such as displays or protective cases—the best construction adhesive for aluminum to wood might be something like epoxy-based products known for their durability and resistance to moisture over time. Ultimately, selecting an appropriate option from available Blister Pack Adhesives requires careful consideration of project requirements alongside thorough research into product performance ratings.
Types of Adhesives for Aluminum Blisters
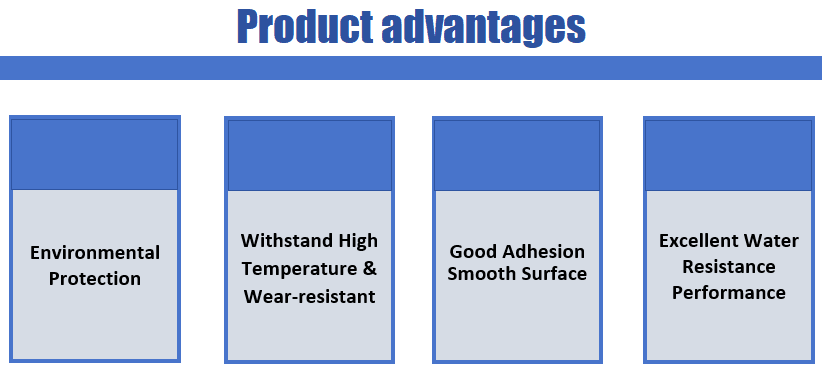
When it comes to selecting the right adhesive for aluminum blisters, there are several options available, each with unique properties and applications. Understanding these different types can help you determine what is best suited for your specific needs. In this section, we will explore water-based adhesives, high-strength adhesives, and construction adhesives that effectively bond aluminum to wood.
Water-Based Adhesive Liquid Sealant Polyurethane Blister
Water-based adhesive liquid sealants, particularly polyurethane formulations, are gaining popularity in the blister packaging industry due to their environmental benefits and strong bonding capabilities. These adhesives offer excellent flexibility and durability while being less harmful than solvent-based alternatives. When considering an adhesive for aluminum blister applications, water-based polyurethane provides a reliable option that meets both performance and eco-friendly criteria.
Using a water-based adhesive liquid sealant polyurethane blister can significantly enhance the sealing process of blister packs while ensuring product safety. They create a robust bond that withstands various environmental conditions without compromising on adhesion strength or flexibility. Plus, they are easy to apply and clean up—making them a favorite among manufacturers looking for efficiency without sacrificing quality.
Overall, if you're asking yourself what is the best adhesive for aluminum?, look no further than water-based polyurethane options that combine effectiveness with sustainability in your packaging solutions.
Comparing High-Strength Adhesives for Aluminum
When it comes to high-strength adhesives suitable for aluminum applications, there are several contenders worth comparing. A high strength adhesive for aluminum must not only provide exceptional bonding capabilities but also maintain performance under stress or extreme conditions. Epoxy and cyanoacrylate (super glue) are two popular choices that stand out due to their superior strength and versatility.
Epoxy adhesives generally offer outstanding resistance to moisture and heat while providing robust structural integrity—ideal when sealing blister packs containing medical supplies or sensitive products. On the other hand, cyanoacrylate offers rapid curing times which can be beneficial in fast-paced production environments where time is of the essence when sealing blister packs effectively.
Ultimately, when assessing what is a high strength adhesive for aluminum?, consider factors such as curing time, environmental resistance, and application method to find the right match for your specific project needs.
Best Construction Adhesive for Aluminum to Wood
Finding the best construction adhesive for aluminum to wood involves understanding how different formulations perform under various conditions. Many professionals recommend using polyurethane construction adhesives because they create strong bonds between dissimilar materials like metal and wood while allowing some flexibility in joint movement over time. This feature is crucial when working on projects where temperature fluctuations may occur.
Another viable option includes hybrid polymer adhesives which combine the strengths of both silicone and polyurethane technologies—offering excellent adhesion properties along with moisture resistance ideal for outdoor applications or situations involving varying humidity levels. When deciding on an adhesive solution that meets your requirements, consider factors such as ease of application and drying times alongside bonding strength.
So if you're pondering what is the best construction adhesive for aluminum to wood?, remember that both polyurethane and hybrid polymer options provide reliable solutions tailored specifically towards achieving lasting results in diverse environments.
Eco-Friendly Adhesive Solutions
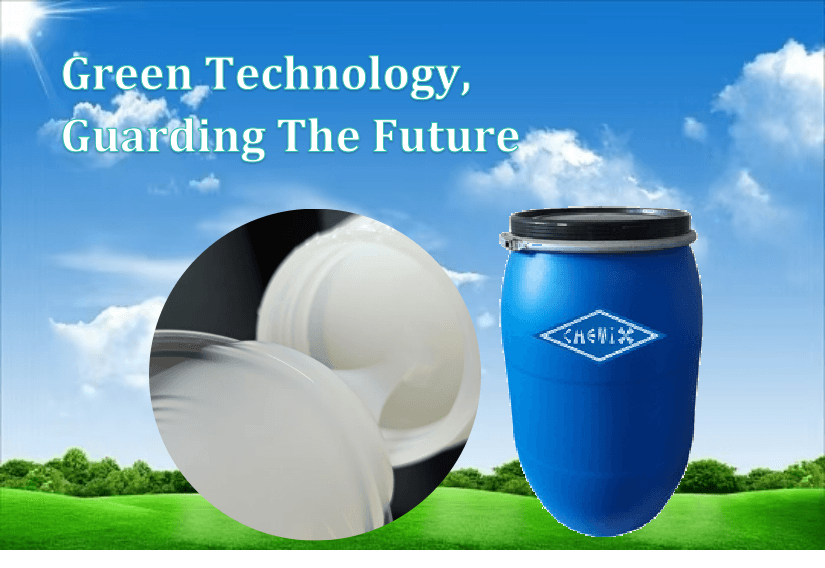
In an era where sustainability is more than just a buzzword, the adhesive industry is stepping up with innovative solutions that cater to both performance and environmental responsibility. One such solution is Chemix's water-based resin, which offers a remarkable alternative to traditional solvents. This eco-friendly adhesive for aluminum blister packs not only meets stringent safety standards but also minimizes harmful emissions during production and application.
Benefits of Chemix's Water-Based Resin Solution
Chemix's water-based resin solution stands out as an excellent choice for those seeking high-quality adhesive for aluminum blister applications. It provides strong bonding capabilities without the harsh chemicals found in many conventional adhesives, making it safer for both users and the environment. Furthermore, this type of adhesive exhibits impressive flexibility and durability, ensuring that your blister packaging remains intact throughout its lifecycle.
When considering what is the best adhesive for aluminum, Chemix’s offering shines due to its ease of application and cleanup. Unlike solvent-based options that can be challenging to work with, water-based adhesives simplify the sealing process of blister packs while ensuring strong adhesion. This makes it ideal for manufacturers who prioritize efficiency without compromising on quality or safety.
How Eco-Friendly Options Impact Packaging
The transition to eco-friendly adhesive solutions significantly influences packaging practices across various industries, particularly in pharmaceuticals and consumer goods. By utilizing sustainable adhesives like Chemix's water-based option, companies can reduce their carbon footprint while still achieving reliable performance in blister pack adhesives. This shift not only appeals to environmentally conscious consumers but also aligns businesses with growing regulatory demands for greener practices.
Moreover, using eco-friendly adhesives can enhance brand reputation as companies demonstrate their commitment to sustainability. As customers increasingly seek products from brands that prioritize environmental responsibility, adopting these innovative solutions can lead to improved market positioning. In turn, this creates a win-win situation where businesses thrive while contributing positively to the planet.
Innovations in Sustainable Adhesive Technologies
The landscape of adhesive technology is evolving rapidly with exciting innovations aimed at enhancing sustainability without sacrificing effectiveness. New formulations are emerging that combine high-strength properties suitable for aluminum applications with environmentally friendly components—think water-based adhesive liquid sealant polyurethane blister formulations designed specifically for demanding environments.
What is a high strength adhesive for aluminum? The latest advancements ensure that these sustainable options meet rigorous performance standards typically associated with traditional adhesives while being kinder to our planet’s resources. As research continues into biobased materials and smart adhesives that respond dynamically to their environment, manufacturers are better equipped than ever before to create packaging solutions that are both effective and eco-conscious.
Troubleshooting Common Adhesive Issues
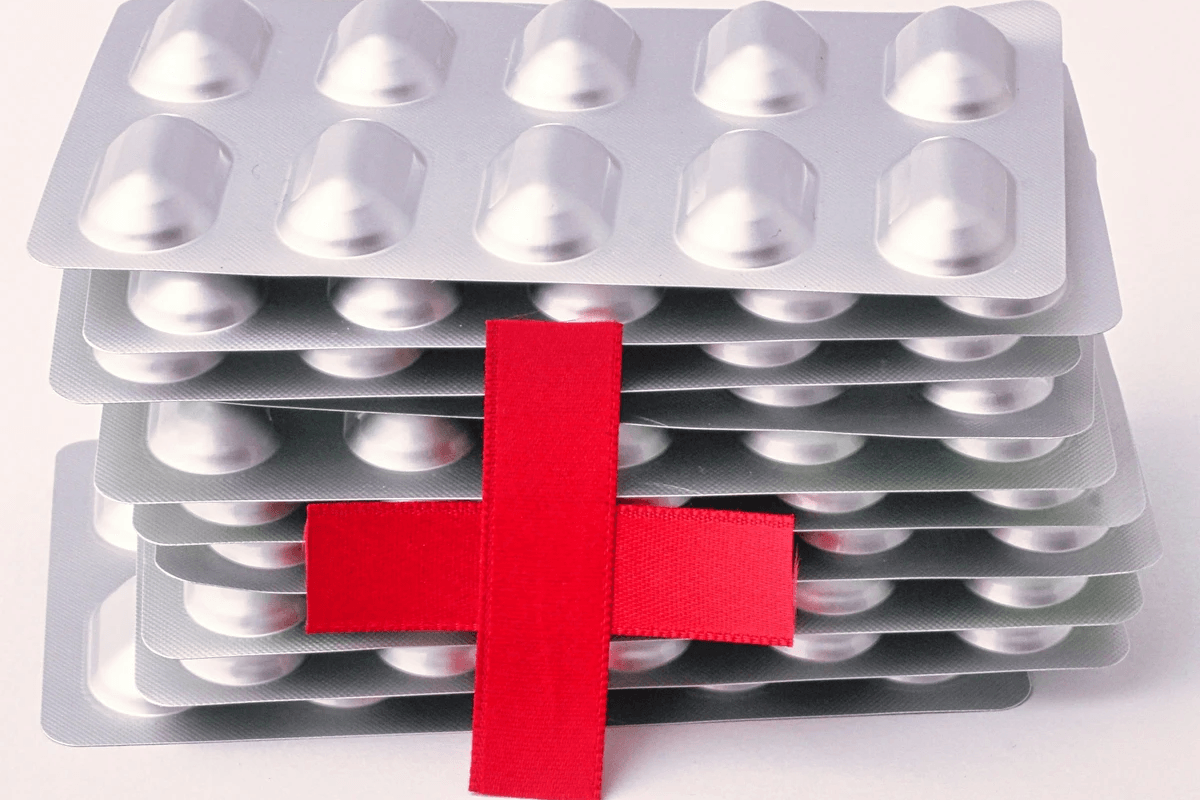
When working with blister pack adhesives, issues can arise that hinder the packaging process. Understanding these common problems is essential for ensuring that your adhesive for aluminum blister applications performs effectively. By identifying the root causes of adhesive failures, you can take proactive measures to avoid them in the future.
Common Problems with Blister Pack Adhesives
One of the most frequent issues encountered with blister pack adhesives is inadequate adhesion, which can lead to product leakage or damage. This often occurs when the surface is not properly cleaned or prepped before applying the adhesive for aluminum blister packs. Additionally, environmental factors such as humidity and temperature fluctuations can negatively affect adhesive performance, making it crucial to monitor these conditions during application.
Another common problem is delamination, where layers of materials separate due to insufficient bonding strength. Selecting what is a high strength adhesive for aluminum can mitigate this risk significantly; however, using an inappropriate type may result in poor performance under stress or temperature changes. Furthermore, improper curing time or conditions may prevent the adhesive from achieving its full bonding potential, leading to compromised integrity.
Lastly, contamination from dust or oils on surfaces can also cause adhesion failures. Ensuring that surfaces are clean and free from any contaminants before applying your chosen adhesive will enhance the overall effectiveness of your blister pack adhesives. To avoid these pitfalls, always follow manufacturer guidelines on preparation and application.
How to Seal a Blister Pack Effectively
Sealing a blister pack effectively requires precision and attention to detail throughout the process. First and foremost, ensure that you select what is best adhesive for aluminum based on your specific needs—this could include water-based adhesive liquid sealant polyurethane blister options known for their eco-friendliness and strong bonding capabilities. Once you've chosen your adhesive wisely, prepare both surfaces by cleaning them thoroughly with an appropriate solvent.
Next comes the application phase: apply a uniform layer of your selected adhesive for aluminum blister onto one surface while ensuring not to overapply it—too much can lead to oozing during sealing! Align both components carefully and apply consistent pressure across the entire area until secure; this will help achieve optimal adhesion without compromising package integrity. Finally, allow adequate curing time as specified by your chosen product's instructions; this step cannot be overlooked if you want long-lasting results.
Regularly checking seals after production is also essential in maintaining quality control standards in packaging processes involving blister packs. If any flaws are detected post-sealing—such as weak bonds or visible gaps—it may indicate that adjustments need to be made regarding either material choice or sealing technique moving forward.
What to Do if Adhesives Fail
If you find yourself facing an unfortunate scenario where adhesives fail during use or production stages—don’t panic! Start by assessing what went wrong: was it due to improper surface preparation? Or perhaps environmental factors played a role? Identifying whether you used an appropriate high-strength adhesive for aluminum will provide insights into how best to remedy future issues.
In cases where failure has occurred post-application but before reaching consumers' hands—consider implementing a quality assurance protocol that includes regular checks on seal integrity throughout production runs moving forward! This proactive approach helps catch potential problems early before they escalate into larger concerns down the line regarding product safety and efficacy.
If all else fails despite following best practices diligently—the solution might involve revisiting your choice of materials altogether! Investigate whether switching out current options for alternatives like water-based adhesives could yield better results while contributing positively toward sustainability efforts within packaging industries today!
Conclusion
In the world of blister packaging, the significance of selecting the right adhesive cannot be overstated. As we move forward, advancements in adhesive technologies will shape how products are packaged, especially in medical applications where safety and efficacy are paramount. Understanding trends such as eco-friendly options and high-strength adhesives will help manufacturers stay ahead in a competitive market.
Future Trends in Blister Packaging Adhesives
The future of blister pack adhesives is leaning towards sustainability and enhanced performance. Innovations like Water-Based Adhesive Liquid Sealant Polyurethane Blister are gaining traction for their environmental benefits without compromising on strength or durability. Additionally, as manufacturers seek to optimize production efficiency, high-strength adhesives for aluminum will become more essential, ensuring that packages remain secure while being easy to open.
The Impact of Adhesives on Medical Safety
Adhesives play a crucial role in maintaining medical safety by ensuring that products remain sterile and uncontaminated until they reach the end user. Choosing the right adhesive for aluminum blister packs can prevent leaks or contamination that could compromise product integrity. Consequently, understanding what is the best adhesive for aluminum not only impacts packaging aesthetics but also has direct implications for patient health and safety.
Choosing the Right Adhesive for Your Needs
Questions like What is a high strength adhesive for aluminum? or What is the best construction adhesive for aluminum to wood? must be addressed based on specific use cases and requirements. Ultimately, knowing how to seal a blister pack effectively with the right type of blister pack adhesives can make all the difference between a successful product launch and one fraught with issues.