Introduction
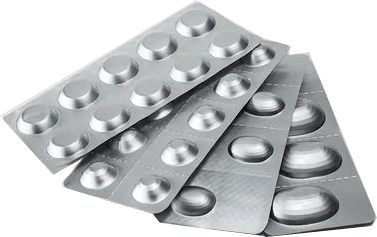
Understanding Blister Packaging
Blister packaging typically consists of a pre-formed plastic cavity or pocket that holds the product securely in place, often sealed with a backing material like aluminum or paperboard. This design ensures that items remain safe from moisture and contamination while also allowing for easy visibility and access for consumers. When discussing glue for aluminum blister packs, it's essential to consider how the adhesive interacts with both the plastic and aluminum components to achieve optimal performance.
The Importance of Strong Adhesives
Strong adhesives are the unsung heroes behind effective blister packaging; they ensure that the package remains intact throughout its lifecycle, from manufacturing to consumer use. Without reliable bonding agents, even the best-designed blister packs can fail at critical moments—leading to product spoilage or damage. Therefore, understanding what glue is best for aluminum is key; selecting an adhesive that provides durability while meeting industry standards is paramount.
Overview of Glue for Aluminum Blister
When it comes to choosing glue for aluminum blister applications, it's important to delve into various options available on the market today. From FDA-approved medical blister adhesives to more general-purpose solutions, each type has its own strengths and weaknesses depending on the intended use case. By exploring these options further, we can better answer questions like “What adhesive is used in blister packaging?” and “How to seal a blister pack?” effectively while ensuring quality and safety standards are met.
Types of Glue for Aluminum
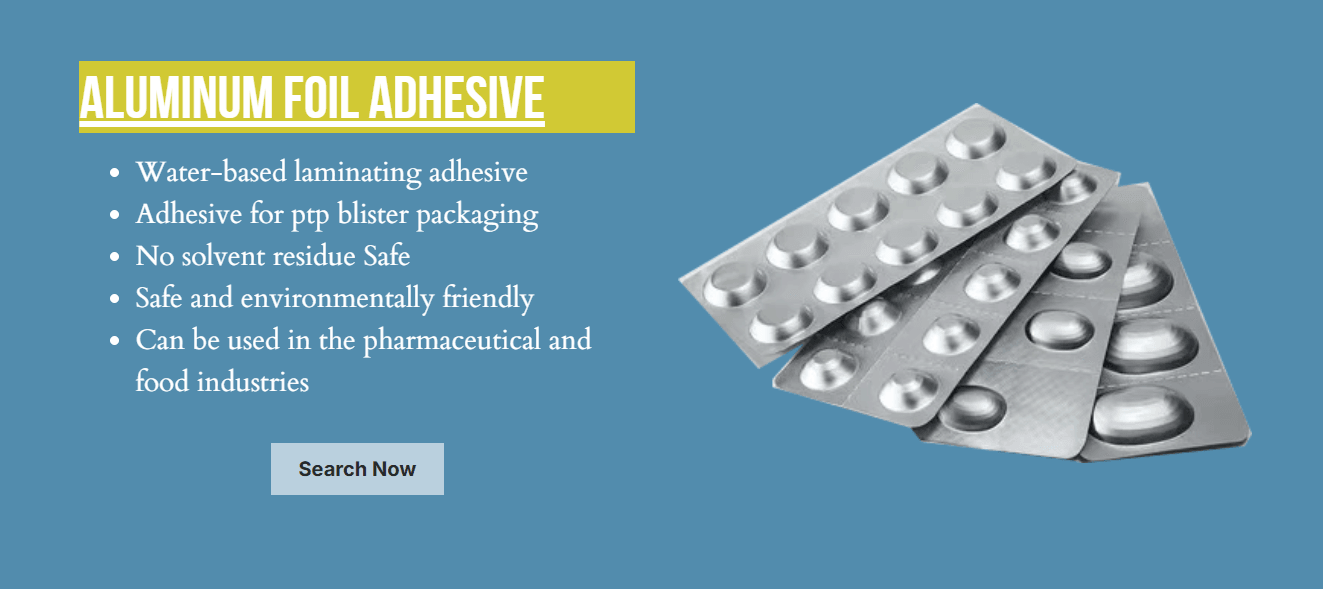
Choosing the Right Adhesive
Choosing the right adhesive for aluminum blister packaging involves considering several factors such as bonding strength, curing time, and environmental impact. For instance, if you’re pondering What glue is best for aluminum?, water-based adhesives often emerge as top contenders due to their lower toxicity and ease of use. Additionally, understanding what adhesive is used in blister packaging can guide you toward options that have been proven effective in similar applications.
When selecting glue for aluminum blister packs, it's vital to consider the specific requirements of your project—whether it's a medical application requiring FDA-approved materials or a general manufacturing need. Each adhesive type has its unique properties that cater to different scenarios; hence thorough research will lead you to the best solution tailored to your needs.
Exploring FDA-Approved Options
For industries dealing with sensitive products like pharmaceuticals or food items, exploring FDA-approved options is non-negotiable when discussing glue for aluminum blister packaging. These adhesives are rigorously tested to ensure they meet safety standards while providing strong bonding capabilities essential for product integrity. When asking What is the best glue for aluminum to wood? in a mixed-material context, knowing whether an adhesive complies with FDA regulations becomes even more critical.
FDA-approved medical blister adhesives are designed not only to bond effectively but also to withstand various environmental conditions without compromising safety or performance. This makes them particularly suitable when sealing sensitive items that require optimal protection from external elements while maintaining regulatory compliance.
Comparing Strengths and Weaknesses
Comparing strengths and weaknesses among different types of adhesives can help clarify which option stands out as superior for your specific needs regarding aluminum blister applications. For example, traditional solvent-based glues may offer unmatched bonding strength but often come with drawbacks like longer drying times and potential health risks due to volatile organic compounds (VOCs). On the other hand, water-based solutions are increasingly popular due to their eco-friendliness and ease of application—perfectly aligning with modern sustainability trends.
Additionally, when evaluating what adhesive is used in blister packaging across various industries, one must consider factors such as temperature resistance and flexibility after curing; these characteristics significantly influence long-term performance and reliability of the bond formed by these adhesives. Ultimately, knowing how each type measures up against your project requirements will empower you in making an informed decision that balances performance with safety.
What Glue is Best for Aluminum?
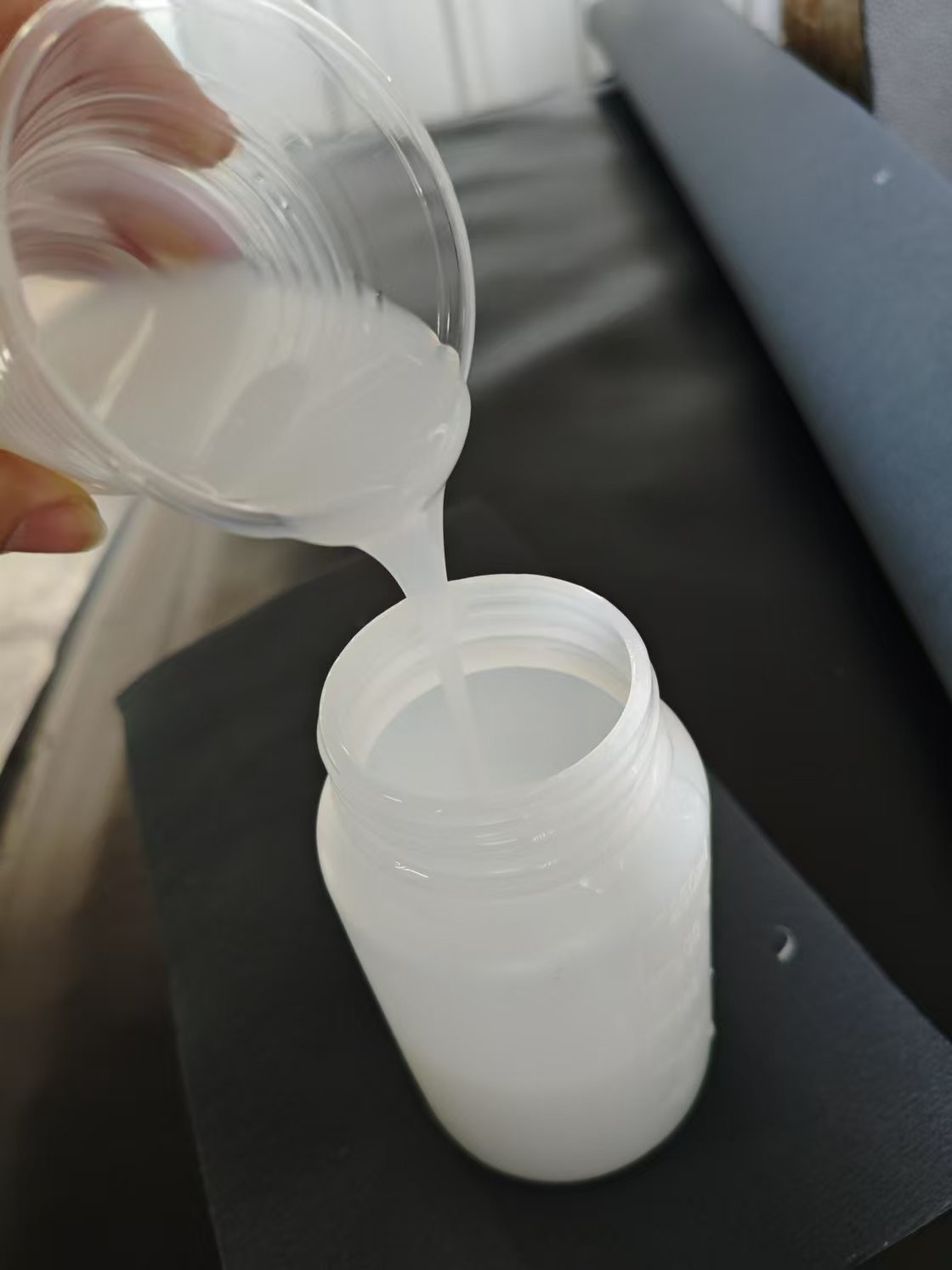
Examining Popular Adhesives
Several adhesives stand out when considering glue for aluminum blister applications. Epoxy adhesives are renowned for their strength and durability, making them a popular choice for industrial uses. However, if you're looking for a more flexible option, polyurethane glues offer excellent versatility and can bond dissimilar materials effectively.
Another contender in the race of What adhesive is used in blister packaging? is acrylic-based glue, which provides quick bonding time and good resistance against various environmental factors. Each type of adhesive presents its own strengths and weaknesses; thus, understanding your specific application will help you choose the most suitable option. Ultimately, whether you're sealing medical products or consumer goods in blister packs, finding the right adhesive ensures reliability and effectiveness.
Chemix's Water-Based Resin Solution
For those seeking an environmentally friendly alternative, Chemix's water-based resin solution has emerged as a game-changer in the realm of aluminum adhesives. This innovative product not only adheres well to aluminum but also meets FDA requirements for safety—making it ideal for medical blister adhesive applications. With low VOC emissions and easy cleanup with water, this solution caters to both health-conscious consumers and eco-friendly manufacturers.
Moreover, Chemix’s formulation offers impressive bonding capabilities while remaining gentle on surfaces—a crucial factor when considering how to seal a blister pack effectively without damaging its contents or structure. The versatility of this resin allows it to be used across various industries while ensuring that safety standards are met without compromising performance. In short, if you’re asking “What glue is best for aluminum?” look no further than Chemix’s remarkable offering.
The Role of Surface Preparation
No matter how great your chosen adhesive may be, surface preparation plays an essential role in achieving optimal results when working with aluminum surfaces. Proper cleaning removes contaminants such as dust or grease that could hinder adhesion; thus ensuring that your glue bonds effectively is key to success! Techniques like sanding or using solvents can enhance surface roughness—creating more area for the adhesive to grip onto.
Additionally, priming surfaces before applying your chosen glue can significantly improve bond strength; especially important when dealing with challenging materials like metal or wood combinations (think about “What is the best glue for aluminum to wood?”). Remember: taking time during surface preparation will pay off later by providing a durable bond that stands up against wear over time—especially critical in applications involving medical blister adhesives where reliability is paramount.
Blister Pack Adhesives Explained
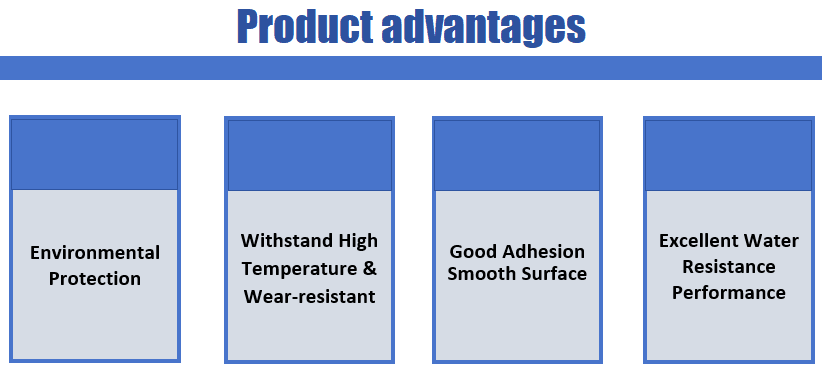
The right glue for aluminum blister packs not only secures the contents but also ensures compliance with industry standards, especially in medical applications. Understanding what adhesive is used in blister packaging can make a significant difference in performance.
What Adhesive is Used in Blister Packaging?
In blister packaging, various adhesives are utilized depending on the materials involved and the intended use of the package. Commonly, heat seal adhesives are employed, which bond plastic to aluminum or other substrates upon application of heat and pressure. Additionally, medical blister adhesive options are specially formulated to meet stringent regulatory requirements while providing a reliable seal that protects sensitive products.
Characteristics of Effective Blister Pack Adhesives
Effective blister pack adhesives must exhibit several key characteristics to ensure optimal performance. First and foremost, they should provide strong adhesion to both aluminum and plastic surfaces, ensuring that the packages remain intact during handling and transport. Furthermore, these adhesives should be resistant to moisture and temperature variations; this is particularly important for products that may be exposed to challenging environments or require a long shelf life.
Another vital characteristic is compatibility with various materials used in blister packs—this includes not only aluminum but also PVC, PETG, and other thermoplastics commonly found in packaging solutions. The best glue for aluminum blister applications will also demonstrate quick curing times while maintaining flexibility once set; this ensures that any movement or stress does not compromise the bond.
Application Techniques for Optimal Bonding
To achieve a professional finish when sealing a blister pack, employing proper application techniques is essential. Start by ensuring that all surfaces are clean and dry; this will help maximize adhesion when applying your chosen glue for aluminum blisters. Depending on the adhesive type being used—whether it's a spray-on adhesive or a liquid glue—follow specific instructions regarding application thickness and method.
Once applied, it's crucial to apply consistent pressure during the bonding process; using specialized tools like heat sealers can enhance effectiveness significantly by evenly distributing heat across both surfaces being bonded together. Additionally, knowing how to seal a blister pack properly involves timing: allowing adequate curing time before handling ensures durability without compromising product integrity.
How to Seal a Blister Pack?
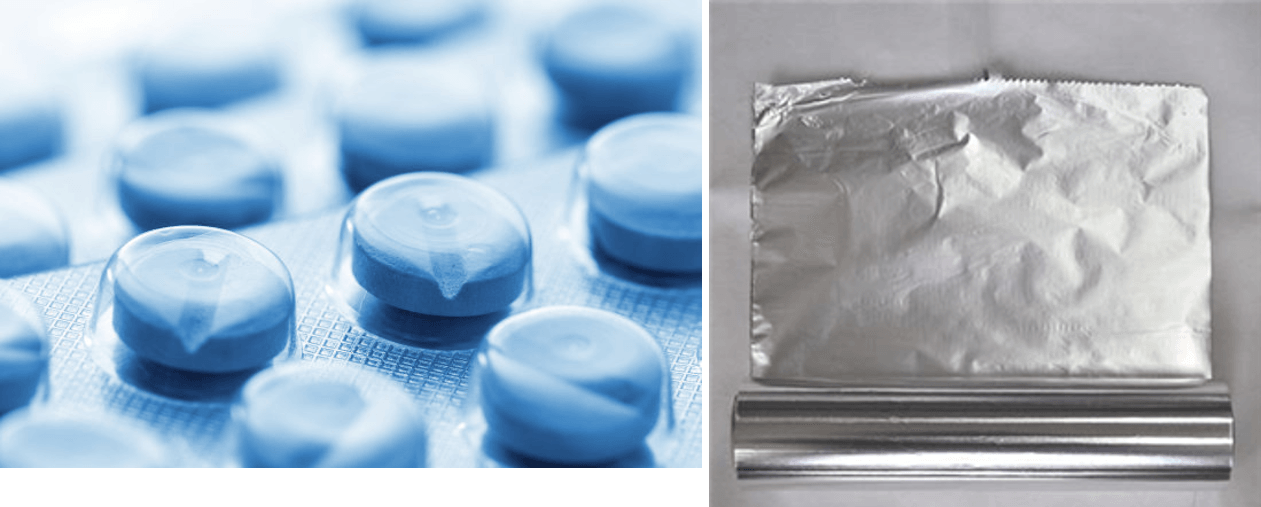
Sealing a blister pack is an essential process that ensures the product remains protected and tamper-proof. Understanding the methods and materials involved will help you achieve a secure seal, especially when using glue for aluminum blister applications. With the right approach, you can create professional-quality packaging that meets industry standards.
Step-by-Step Sealing Methods
To effectively seal a blister pack, start by preparing your workspace to ensure cleanliness and efficiency. First, position the aluminum blister and the backing material correctly; this alignment is crucial for achieving an optimal bond. Next, apply your chosen adhesive—whether it’s a medical blister adhesive or another type—along the edges of the aluminum blister before pressing down firmly onto the backing material.
Once pressed together, allow sufficient time for curing based on your adhesive’s specifications. If you're wondering what glue is best for aluminum?, consider options that offer strong adhesion while being safe for your specific product type. Finally, inspect the sealed area to ensure there are no gaps or bubbles; if any are found, reapply pressure as needed.
Tools You Will Need
To seal a blister pack efficiently, gather some essential tools beforehand. You'll need a heat source if you're using heat-activated adhesives; this could be an industrial heat sealer or even a basic iron in some cases. Additionally, having precision applicators for glue will help you control how much adhesive goes on your aluminum blister without making a mess.
Don’t forget about protective gear such as gloves and goggles to keep yourself safe from any fumes or spills associated with adhesives like medical blister adhesive. Lastly, having scissors or cutting tools handy will allow you to trim excess materials after sealing if necessary—ensuring that everything looks neat and professional.
Tips for Achieving a Professional Finish
Achieving that polished look in your sealed blister pack comes down to attention to detail and technique. Start by ensuring all surfaces are clean; dust or grease can impede adhesion significantly when working with glue for aluminum blisters. When applying pressure during sealing, use even force across the entire surface area; this helps avoid weak spots where moisture might seep in later.
Also consider temperature control during sealing; too hot can warp materials while too cold may not activate adhesives properly—finding that sweet spot is key! Remember to test different types of adhesives as well: knowing what adhesive is used in blister packaging can guide you toward making informed decisions about which products yield the best results for various applications.
What is the Best Glue for Aluminum to Wood?
Key Considerations for Mixed Materials
When dealing with mixed materials like aluminum and wood, there are several key factors to consider. First, the differences in expansion rates between metal and wood can lead to stress on the adhesive over time, so it's essential to choose a glue that accommodates these changes. Additionally, surface preparation plays a critical role; clean both surfaces thoroughly to maximize adhesion and ensure that any oils or residues don’t interfere with your chosen glue for aluminum blister applications.
Another important consideration is the environment in which your bonded materials will exist. If they’ll face moisture or temperature fluctuations, opt for adhesives designed specifically for such conditions. Lastly, understanding how each adhesive interacts with both surfaces will guide you toward making an informed choice.
Recommended Adhesives for Metal-Wood Bonds
For bonding aluminum to wood effectively, several adhesives stand out as top contenders. Epoxy adhesives are highly regarded due to their exceptional strength and versatility; they create robust bonds that withstand various environmental conditions. Another excellent option is polyurethane glue; it expands as it cures, filling gaps between surfaces while providing impressive durability.
If you're looking for something more specialized, consider medical blister adhesives that offer superior performance in high-demand applications—ideal if your project requires stringent safety standards or FDA approval. Ultimately, experimenting with different types of glue may lead you to discover what works best in your specific scenario.
Testing Adhesive Performance
Once you've selected your adhesive, testing its performance is crucial before committing fully to your project. Conducting small-scale tests allows you to evaluate how well the chosen glue adheres under various conditions—this step can save you from potential headaches later on when trying to seal a blister pack or complete another task requiring strong bonds.
Consider applying weights or exposing samples to moisture and temperature changes during testing phases; this helps gauge long-term performance effectively. Remember that even the best glue for aluminum blister applications may not perform well without proper surface treatment and application techniques—so never skip those steps!
Conclusion
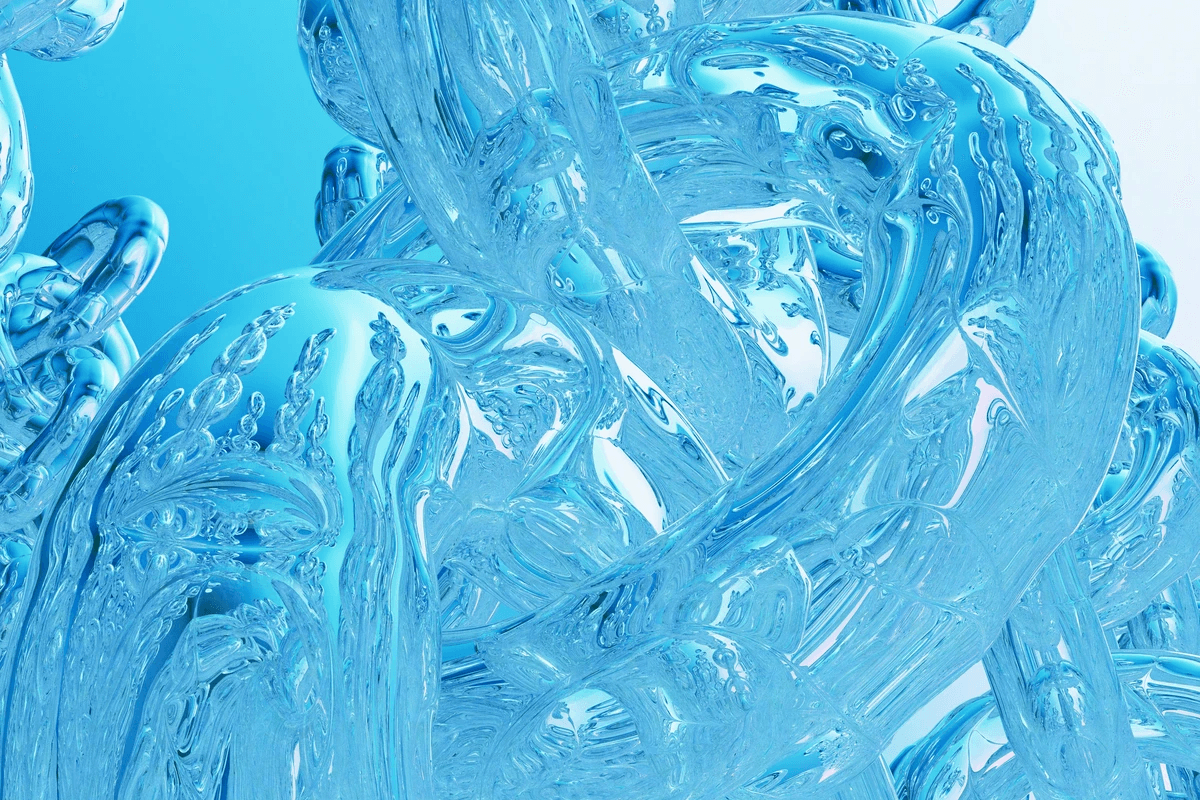
Best Practices for Choosing Adhesive
When selecting glue for aluminum blister packaging, consider factors such as adhesion strength, drying time, and compatibility with your materials. It's crucial to ask yourself: What adhesive is used in blister packaging? This knowledge will help you navigate through FDA-approved options and identify adhesives that meet industry standards. Always test your chosen adhesive on sample materials before full-scale application to ensure it meets your requirements.
Environmental Benefits of Water-Based Solutions
Water-based adhesives are gaining traction due to their eco-friendly composition and reduced VOC emissions compared to solvent-based alternatives. By opting for these solutions in aluminum blister packaging, manufacturers can contribute to a greener planet while still maintaining strong adhesion properties. The environmental benefits extend beyond just reducing harmful chemicals; they also often provide excellent performance in medical blister adhesive applications.
Future Trends in Blister Packaging Adhesives
As technology advances, we can expect exciting developments in blister pack adhesives that enhance performance and sustainability. Innovations may include smart adhesives that respond dynamically to environmental changes or improved formulations for better bonding across mixed materials like metal and wood—what is the best glue for aluminum to wood? Additionally, with growing awareness around environmental issues, future trends will likely focus on more biodegradable options that do not compromise on quality or efficiency.